Polystyrene (PS) is a widely used thermoplastic in daily life and industrial fields, known for its lightweight, transparency, ease of processing, and low cost.
From disposable tableware to electronic product casings, from food packaging materials to building insulation panels, PS plastic plays an important role in modern society due to its diverse properties.
However, with the deepening concept of sustainable development, the environmental impact and recycling challenges of PS plastic have also attracted widespread attention.
This article will delve into the chemical structure, physical properties, main application areas, and the opportunities and challenges of polystyrene plastic in sustainable development, providing readers with a comprehensive understanding of this versatile material.
What Is Polystyrene?
Polystyrene (PS) is a thermoplastic polymer synthesized by the free radical polymerization of styrene monomers, with the chemical formula (C8H8)n.
It is a colorless and transparent thermoplastic plastic with a glass transition temperature above 100°C, possessing excellent thermal insulation, electrical insulation, and optical transparency properties.
Thanks to these characteristics, PS is widely used in acrylic glass, ABS resin, electronic and electrical housings, as well as other engineering plastics fields, making it an indispensable material in modern industry.
The discovery and development of polystyrene have a long history. In 1839, German chemist Eduard Simon first isolated polystyrene from natural resin.
In the early 20th century, the commercial production of polystyrene gradually began: in 1930, the German company BASF started industrial production of PS; in 1934, the American company Dow Chemical began producing PS; and in 1954, Dow Chemical further introduced expanded polystyrene foam, greatly expanding the application range of polystyrene .
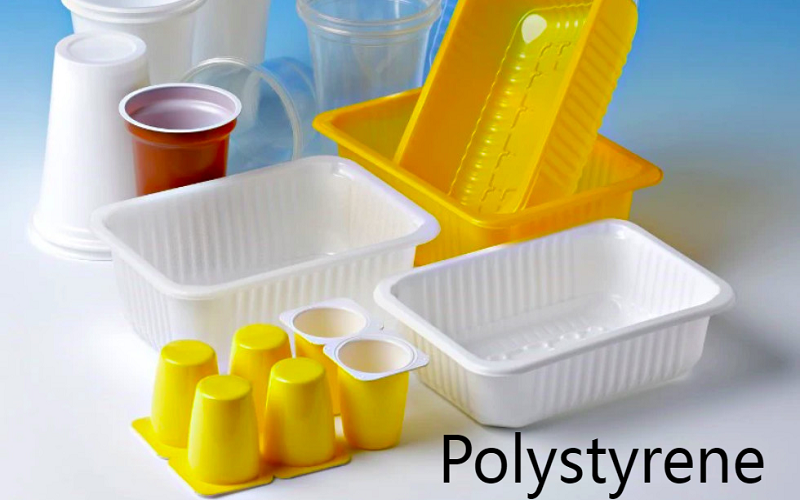
Chemical Structure Of Polystyrene
Polystyrene generally has a head-to-tail structure, with a saturated carbon backbone and side groups consisting of conjugated phenyl rings. This irregular molecular structure increases the rigidity of the molecule, making PS a non-crystalline linear polymer.
Due to the presence of phenyl rings, PS has a relatively high glass transition temperature (Tg) of 80–105°C, making it transparent and hard at room temperature.
The rigidity of the molecular chain also makes it prone to stress cracking. The presence of side phenyl groups increases the chemical reactivity of polystyrene, allowing characteristic reactions such as chlorination, nitration, and sulfonation to occur.
Additionally, the side phenyl groups activate the α-hydrogen atoms on the main chain, making them prone to oxidation in air to form peroxides, which leads to degradation.
Therefore, polystyrene products tend to yellow and become brittle after long-term outdoor exposure. However, the conjugated system of the phenyl rings also provides good radiation resistance, so under strong radiation conditions, the performance changes of the polymer are minimal.
The Properties Of Polystyrene Plastic
Polystyrene is a long chain hydrocarbon, but the carbon atoms in the molecular chain are spaced with large phenyl groups, and this structure determines the special properties of polystyrene.
Mechanical Properties
Polystyrene is a rigid plastic that exhibits brittle fracture under stress. Its inherent brittleness limits its impact resistance, but modifications like high-impact polystyrene (HIPS) can enhance toughness for specific applications.
Thermal Properties
The characteristic temperatures of polystyrene are: a brittle temperature of about -30°C, a glass transition temperature of 80–105°C, a melting temperature of 140–180°C, and a decomposition temperature above 300°C.
Due to the significant decrease in mechanical properties with increasing temperature and its poor heat resistance, the continuous use temperature is around 60°C, and the maximum should not exceed 80°C.
At the same time, PS has a low thermal conductivity of 0.04–0.15 W/(m·K), which is hardly affected by temperature changes, thus providing excellent thermal insulation.
Electrical Properties
Polystyrene exhibits exceptional electrical insulating properties. Its volume resistivity ranges from 10^20 to 10^22 Ω·cm, and surface resistivity is between 10^15 and 10^18 Ω. The dielectric loss tangent is extremely low and remains unaffected by frequency, temperature, or humidity fluctuations.
Chemical Resistance
Polystyrene is resistant to a variety of alkalis, salts, and aqueous solutions, as well as lower alcohols and certain acids. However, it is susceptible to degradation by concentrated nitric acid and other strong oxidizing agents.
Additionally, PS is prone to aging under heat, oxygen, and atmospheric conditions, leading to molecular chain scission and discoloration. The presence of impurities, such as residual monomers or sulfides, accelerates aging, causing yellowing and embrittlement in long-term use.
Optical Properties
Polystyrene boasts excellent optical properties, with a light transmittance of 88–92% and a refractive index of 1.59–1.60. It allows visible light across all wavelengths to pass through, making it one of the most transparent plastics, second only to acrylic polymers like PMMA (organic glass).
Processability
One of polystyrene’s standout features is its excellent processability. It exhibits high thermal stability and superior flowability when molten, enabling easy molding, particularly through injection molding. This makes PS well-suited for large-scale production.
Furthermore, PS has a low molding shrinkage rate and excellent dimensional stability, ensuring precise and consistent molded polystyrene parts.
Polystyrene Properties Table | |
Properties | Reference Value |
Density(g/cm³) | 1.04-1.13 |
Melting Temperature(°C) | 240 |
Glass Transition Temperature(°C) | 80-105 |
Tensile Strength(MPa) | 46-60 |
Water Absorption(%) | 0.03-0.1 |
Electrical Resistivity(Ω·cm) | 10^20~10^22 |
Thermal Conductivity(W/(m·K)) | 0.08 |
Types Of Polystyrene
Below are the primary types of polystyrene, distinguished by their composition and properties:
General-Purpose Polystyrene (GPPS)
General polystyrene resin is a non-toxic, odorless, colorless transparent granule, resembling a glass-like brittle material.
Its products have extremely high transparency, with a light transmittance of over 90%, good electrical insulation properties, easy coloring, good processing fluidity, rigidity, and good chemical corrosion resistance.
The drawbacks of general polystyrene include brittleness, low impact strength, susceptibility to stress cracking, poor heat resistance, and deformation or performance degradation in boiling water.
High-Impact Polystyrene (HIPS)
High-impact polystyrene is a form of polystyrene plastic, produced by graft polymerization of styrene monomers with rubber, or a physical blend of polystyrene and rubber (usually polybutadiene rubber).
It is an easily machined and fabricated impact-resistant, versatile, and economical plastic. Some of the products with the highest levels of flame retardants included toy costume beads, a sushi tray, and kitchen utensils made of HIPS.
Expanded Polystyrene (EPS)
EPS, often referred to as polystyrene foam, is a lightweight, cellular material produced by expanding polystyrene beads using a blowing agent such as pentane, then molding them into various shapes.
Expanded polystyrene scrap can be easily added to products such as EPS insulation sheets and other EPS materials for construction applications
Extruded polystyrene (XPS)
The production of XPS primarily uses granules made by uniformly mixing PS with other additives and extruding them into pellets.
During the extrusion process, a foaming agent is added in the molten plastic stage. Through extrusion molding, calendaring, cooling, and cutting, polystyrene foam boards are obtained.
It is primarily used in construction for insulation in walls, roofs, and floors, as well as in pipe insulation and cold storage facilities.
Syndiotactic Polystyrene (SPS)
Syndiotactic polystyrene has a syndiotactic structure and is produced using metallocene catalysts.Its molecular chains have side phenyl groups evenly spaced on both sides, and this ordered structure gives it superior properties compared to general polystyrene.
It features a high melting point, fast crystallization rate, high elastic modulus, excellent electrical properties, and chemical resistance.
It has broad application prospects in the automotive industry, electronics industry, and industrial packaging fields, and can replace some costly and heavily polluting materials.
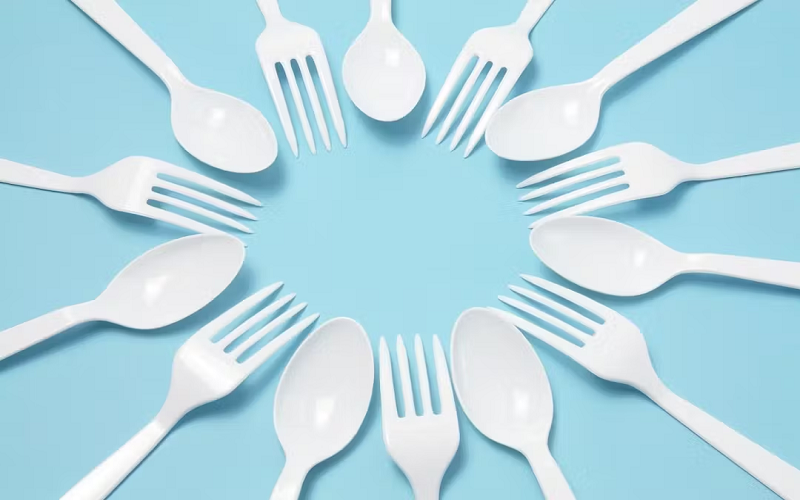
Other Copolymer
Styrene-Acrylonitrile Copolymer (SAN)
SAN stands for Styrene Acrylonitrile, which is a copolymer of styrene and acrylonitrile. It is a colorless and transparent engineering plastic based on polypropylene with relatively high mechanical strength.
The chemical stability of SAN is better than that of polystyrene. SAN products have lower transparency and UV resistance compared to polymethyl methacrylate (PMMA) products but are relatively more affordable.
Acrylonitrile-Butadiene-Styrene Copolymer (ABS)
ABS is a copolymer made from acrylonitrile, butadiene, and styrene. It is characterized by high strength and low weight, making it a stronger material than pure polystyrene.
Styrene-Butadiene-Styrene Copolymer (SBS)
SBS is a triblock copolymer with a structure of polystyrene–butadiene–polystyrene. This material combines the properties of polystyrene and polybutadiene, making it a durable thermoplastic elastomer.
SBS and its various modified forms are used as components to improve impact resistance, flexibility, and flowability in the production of viscous and bend-resistant products such as putty, shoe soles, and roofing felt. SBS is also used to produce transparent impact-resistant polystyrene.
Different Forms Of Polystyrene
Polystyrene plastic is used in different forms, including as foam, film, and rigid plastic, each tailored to specific applications due to variations in structure, additives, or processing methods.
Polystyrene Foam
Polystyrene foam materials mostly use physical foaming agents for foaming, commonly butane, fluorocarbons, carbon dioxide, etc. The density of foamed polystyrene can reach 0.02 to 0.15 g/cm³.
The molding methods for polystyrene foam materials mainly include molding and extrusion. According to the molding method, they can be divided into polystyrene bead foam materials (EPS) and extruded polystyrene foam materials (XPS).
Polystyrene Film
PS pellets are melted and extruded through a die to form flat films or blown into tubular films, which can be further processed (e.g., cut, laminated, or thermoformed) to meet specific requirements. The low shrinkage rate of PS ensures precise film dimensions.
Rigid Polystyrene Plastic
Rigid PS is typically formed via injection molding for complex parts (e.g., casings, containers), extrusion for sheets or profiles, or thermoforming for larger components. Its low molding shrinkage ensures high precision in finished products.
Rigid polystyrene encompasses solid forms of GPPS and HIPS, processed into sheets, molded parts, or extruded profiles for structural or functional applications.
Manufacturing Process Of Polystyrene Material
Two of the most common methods for shaping PS are injection molding and extrusion molding, valued for their efficiency and ability to leverage PS’s excellent flowability and thermal stability when molten. Below is a brief overview of these processes.
Injection Molding
Polystyrene can be injection molded in both solid and foam form.Its low viscosity when melted ensures excellent mold filling, while its low shrinkage rate (0.4–0.8%) results in precise, dimensionally stable parts.
Polystyrene injection molding is used to produce rigid PS parts, such as disposable cutlery, CD cases, and appliance housings (GPPS or HIPS), as well as complex components like medical Petri dishes and electronic casings.
Extrusion Molding
Extrusion is used for PS films (e.g., food packaging, labels), sheets (e.g., for thermoforming trays), and extruded polystyrene foam (XPS) for construction insulation. EPS foam production may also involve extrusion during initial bead formation.
PS’s high melt flowability allows smooth extrusion, producing uniform films or dense foams. The process is continuous, making it cost-effective for large-scale production of consistent shapes.
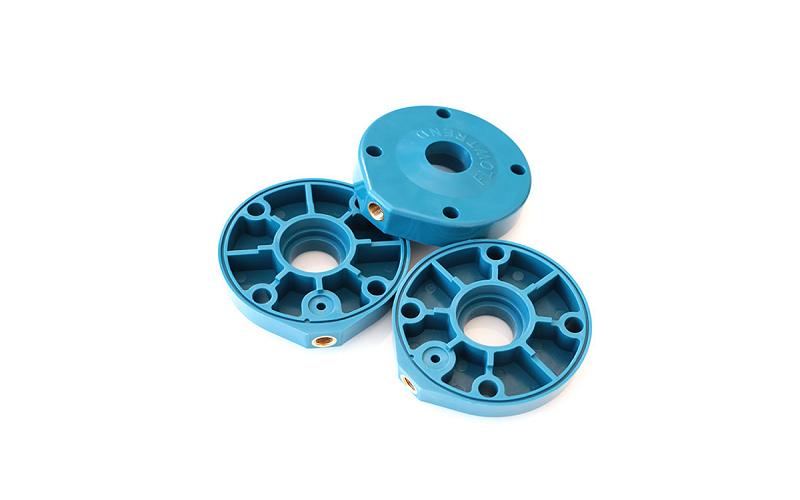
What Are The Uses of Polystyrene Plastic?
Polystyrene is a versatile plastic polymer that is widely used in a variety of industries. It is a hard, brittle plastic that is easily molded into different products, shapes, and foam materials.
Polystyrene plastic finds extensive applications in food packaging, such as disposable cups, plates, and take-out containers, due to its lightweight and insulating properties.
It is also commonly used in the manufacture of medical products like test tubes, petri dishes, and other laboratory equipment because of its clarity and ease of sterilization.
In construction, expanded polystyrene (EPS) and extruded polystyrene (XPS) are widely used for thermal insulation in walls, roofs, and floors, contributing to energy efficiency.
Additionally, polystyrene plastic is used in the production of everyday items such as clothes hangers, CD cases, and various types of plastic packaging.
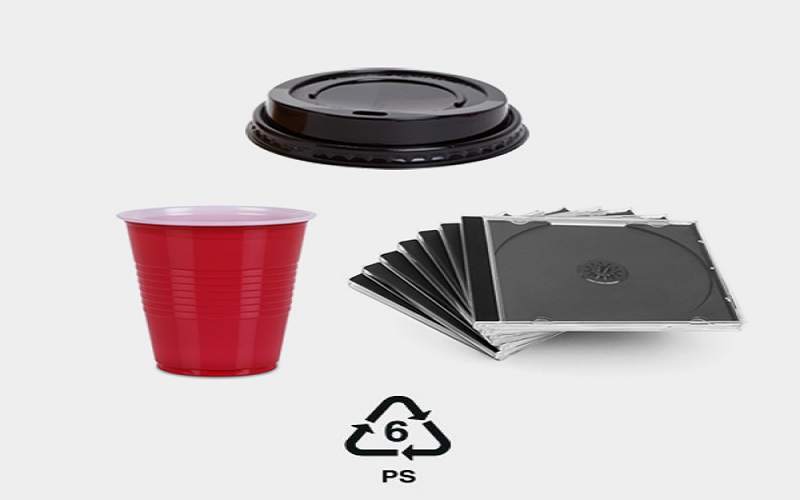
Is Polystyrene Plastic Safe?
“Is polystyrene safe?” has always been a hot topic of public concern. In fact, polystyrene has very low toxicity and is considered one of the hygienic and safe types of plastics.
In daily life, polystyrene products that people come into contact with (such as food containers and packaging materials) usually comply with strict national safety certification standards, such as the Chinese National Standard (GB) or international food contact material regulations.
When the temperature exceeds 60-80°C,styrene molecules may leach out from polystyrene containers into food and be easily ingested by human .
These molecules are not permanently bound to the plastic and can migrate or leach out, exposing consumers when coming in contact with products or when they contaminate indoor air, dust, drinking water, and food.
However, the environmental impact of polystyrene, especially its foam form, is significant. It is non-biodegradable and can persist in the environment for a long period, posing threats to marine animals and ecosystems.
Moreover, exposure to organic solvents and chlorinated solvents can cause polystyrene to degrade, potentially releasing styrene, which raises concerns about potential health risks including toxic effects and adverse effects on human health such as eye irritation and other health problems.
Given these challenges, many regions, including the European Union, have implemented regulations to ban polystyrene packaging in certain applications, especially in food service and packaging, to mitigate its environmental footprint and protect public health.
Overall, while polystyrene plastic remains a commonly used and economical plastic with valuable properties, balancing its utility with sustainability and safety concerns is critical in future development and next projects involving this material.
Can Polystyrene Plastic Be Recycled?
Polystyrene cannot normally be recycled due to its small mass (especially foamed types), low residual value and the fact that it cannot be easily recycled.
Like most plastics, styrofoam is made of a vast cocktail of chemical additives that give it features such as shape, color, texture, etc. These are extremely difficult to separate or break down.It also makes it more difficult to recycle polystyrene plastics.
However, significant improvements have also been made industrially in the reuse of expanded polystyrene, with many new methods developed to densify it.
These methods typically increase its density by 15 slugs/ft³ (29.1 g/cm³) and create suitable centers for recycling operations on clean polystyrene. Some polystyrene manufacturing plants are capable of recycling post-consumer waste expanded polystyrene.
In plastic classification codes, the PS code is 6 (represented by a clockwise triangular arrow symbol), which must be marked on the bottom of the plastic body or packaging to enable proper sorting by consumers and recyclers.
It’s an effective way to reduce plastic pollution and help grow the movement against single use plastics.
Conclusion
Polystyrene plastic is a widely used and economical thermoplastic polymer known for its excellent physical properties, including lightweight, rigidity, and thermal insulation.
Available in different forms such as foam, film, and rigid plastic, it serves diverse applications from food packaging and medical products to construction insulation and consumer goods.
However, its environmental impact, especially in foam form, and potential health risks from styrene exposure have raised concerns. Efforts to improve recycling methods and regulations to limit single-use polystyrene products are important steps toward sustainability.
Understanding both the benefits and challenges of polystyrene is essential for its responsible use and future development in various industries.