Introduction
Plastic spool mold is the most common type of injection molds used to manufacture plastic spools, and they are widely popular in the textile, wire, and cable industries. Plastic spool molds are specifically designed to serve as storage solutions, making the winding, unwinding, and transportation of cables, wires, and other products more convenient and efficient. In this article, we will delve into plastic spool mold, including their mold design, manufacturing process, material selection, specific applications, and how to choose a mold supplier that meets your needs.
The Key Points Of Design For Plastic Spool Mold
The mold design stage is where the shape, size, and features of the spool are determined. This is often done using computer-aided design (CAD) software, allowing for precise control over the design.
The first step is to consider the size and configuration of the plastic bobbin. Determine the size and shape of the plastic bobbin required based on the specific application and the size of the cable or wire to be wound on it. Then consider factors such as the spool’s diameter, width and flange size to ensure that it will accommodate the desired length of cable and provide proper support during winding and unwinding.
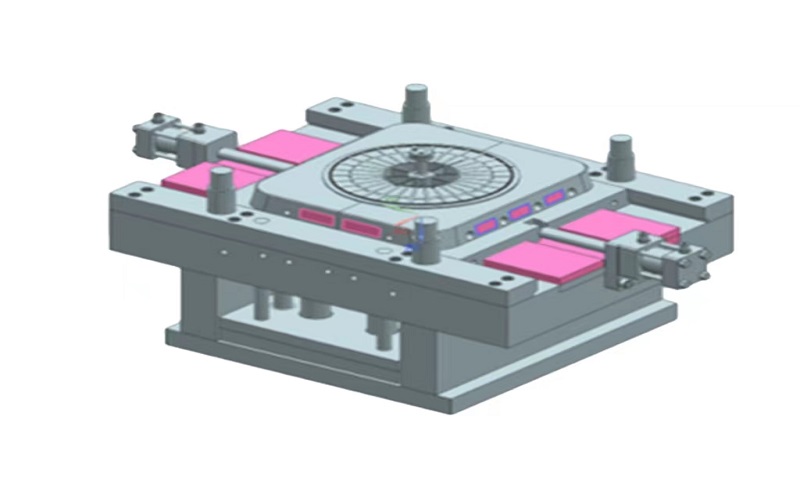
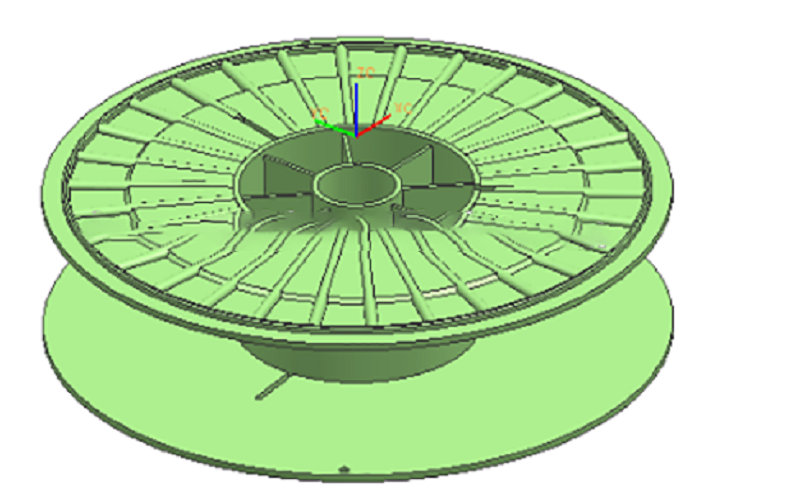
In addition, the strength and durability of the finished product depends on the design of the core and cavity. Create an accurate core and cavity design that incorporates draft angles and ejection to accurately replicate the desired shape of the spool. Consider the shrinkage of the material during the molding process and ensure that the proper allowances are included in the mold design to achieve the desired dimensions of the final molded product.
The third point is that gate and sprue design for plastic spool molds is a key factor in the quality and efficiency of injection molding processes. The optimal gate and sprue system is determined during design to ensure proper material flow and distribution within the mold to minimize defects in the final molded spool.
Components of plastic spool mold
The components of a spool mold are critical elements in the manufacture of plastic spools. A spool mold typically comprises several essential components, including:
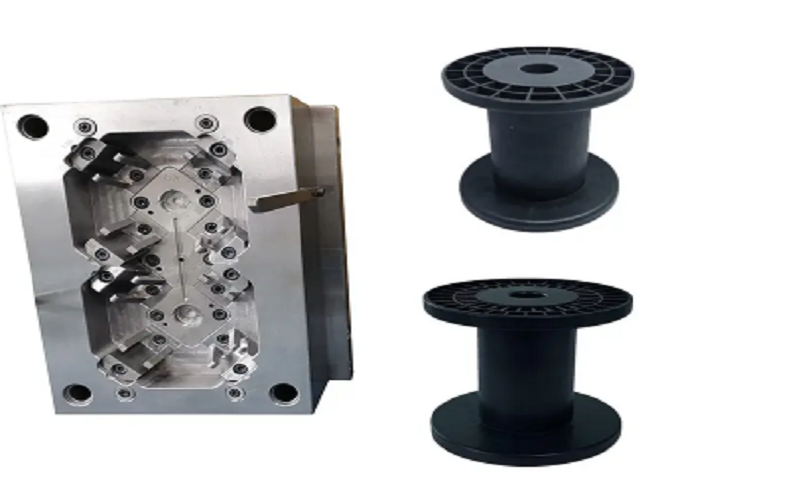
Core
When it comes to manufacturing plastic spools, one of the most crucial components is the core. This internal piece of the spool mold is responsible for creating the hollow center where wires and cables are wound. To ensure the spool can hold the correct amount of material and that the winding process is smooth, the core must be designed to replicate the desired shape and dimensions of the spool’s interior.
Cavity
The cavity component shapes the external surface of the plastic spool. It defines the outer dimensions, features, and contours of the spool. The cavity is precisely machined to achieve the desired appearance and functionality of the spool.
Insert
In some cases, additional inserts may be used in the mold to create specific features or details on the spool. Inserts can be removable components that are placed within the mold to form specific parts of the spool, such as flanges, locking mechanisms, or specialized structures.
Cooling System
The cooling system plays a vital role in the overall mold, including the cooling channels or inserts that effectively manage and regulate the temperature throughout the molding process. It helps solidify the molten plastic and maintains steady cooling for optimal part quality.
Ejection System
The ejection system facilitates the removal of the molded plastic spool from the mold once it has solidified. It may include ejector pins, plates, or other mechanisms that push the spool out of the mold.
Processing details of plastic spool mold
Plastic spool mold processing involves many complex steps, the most critical part of which is the mold core and cavity.
The cavity is the hollow part of the mold that forms the shape of the spool. The cavity is typically created using precision machining methods (usually computer numerical control (CNC) machines or electric discharge machining (EDM)) to ensure that the final plastic spool meets the original design specifications. Once CNC and EDM machining is completed, the mold cavity also needs to be arranged for cooling channels and polishing.
The processing of the coil core is similar to the processing of the cavity.This is the solid part of the mold that forms the shape of the inside of the spool. For more precise machining, we use techniques such as computer numerical control (CNC) machining or electric discharge machining (EDM) to machine the core to ensure that it fits the cavity perfectly and takes the desired shape.
Finally, note the location of the parting line. This is the line where the two halves of the mold – the core and the cavity – intersect. The position of the parting line affects the appearance and strength of the finished bobbin, as well as the life of the mold.
Applications
Plastic spool molds are used in a variety of industries for manufacturing plastic spools, also known as reels, which are cylindrical devices used for storing various types of materials.With the elevated demand for neat packaging and easy storage and transportation of materials in modern manufacturing, the demand for plastic spool mould has increased and has become an essential tool for packaging and shipping companies to wind a variety of materials .
Wire and Cable Industry
Plastic spools are widely used in the wire and cable industry as the preferred solution for storing and winding various types of wire. They are used to wind and store different types of wire, including electrical wire, cable wire and fiber optic cable.
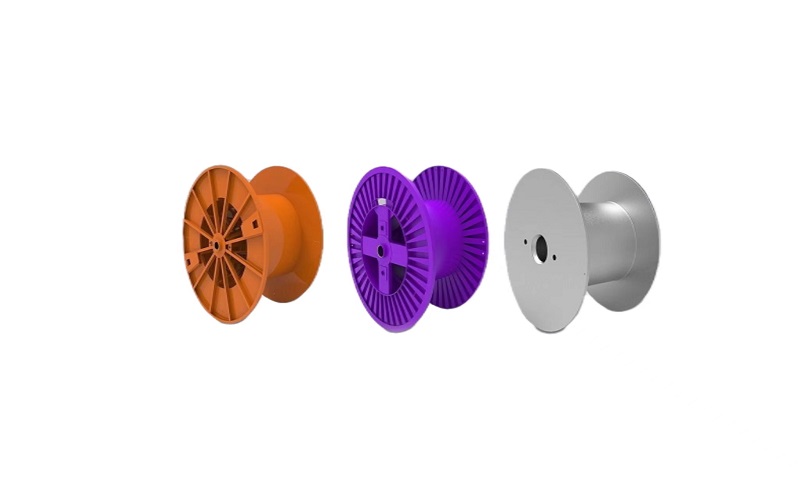
Textile Industry
In the textile industry, plastic spools are ideal for winding and storing cables, yarns and fibers. They are small and light enough to be easily transported and stored, yet strong enough to withstand constant use.
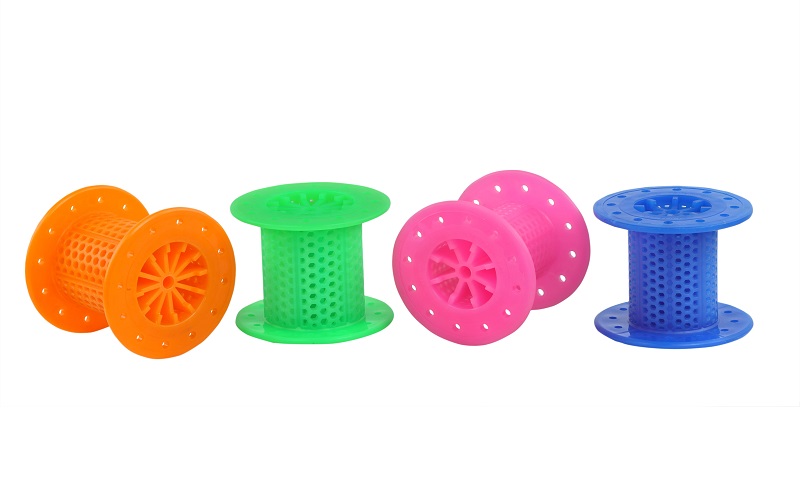
Fishing Industry
Using plastic spool molds, it is possible to produce spools with consistent dimensions and shapes. These plastic spools are designed to be lightweight and durable, making them perfect for carrying in fishing tackle boxes or backpacks. This solves the problem of fishing lines getting tangled frequently, facilitating storage and transportation.
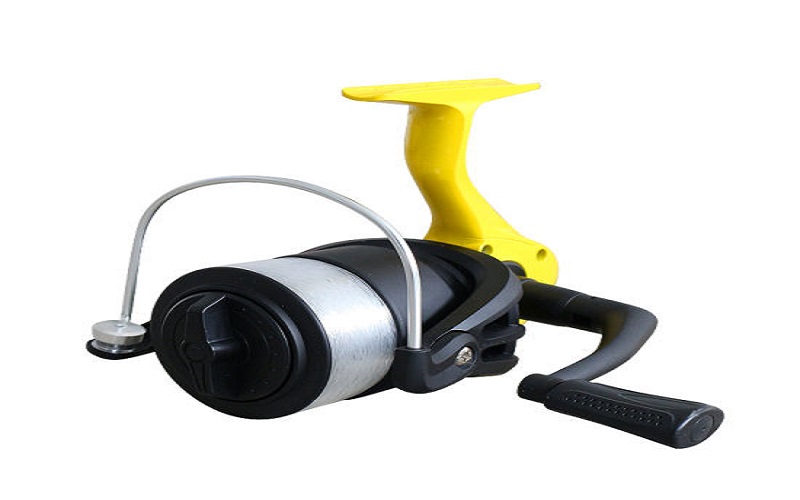
3D Printing
In the 3D printing industry, plastic spool molds are produced to produce spools of wire typically used in order to wind filaments, prevent the plastic filaments used in 3D printers from tangling, and make it easier for them to enter the printer.
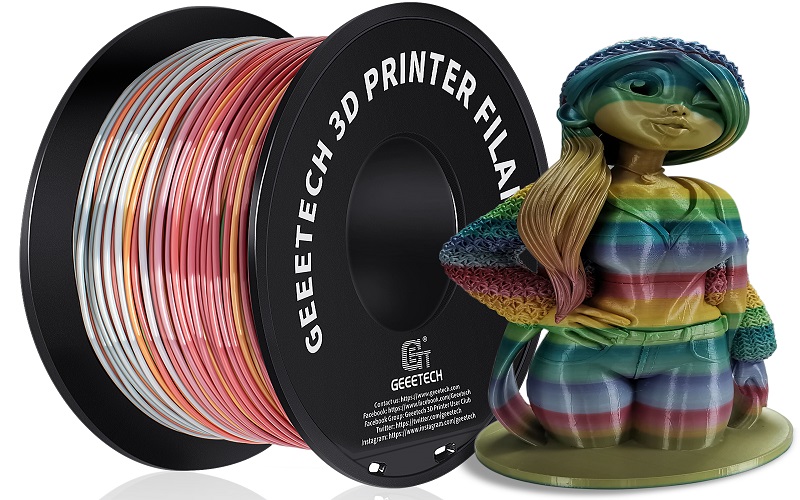
Craft and Decoration
The intricately designed spool molds ensure that the finished plastic bobbins are perfectly shaped and have become an indispensable item for crafts and DIY projects thanks to their durability and flexibility. It can be used to wrap and store decorative materials such as ribbons, lace, or strings.
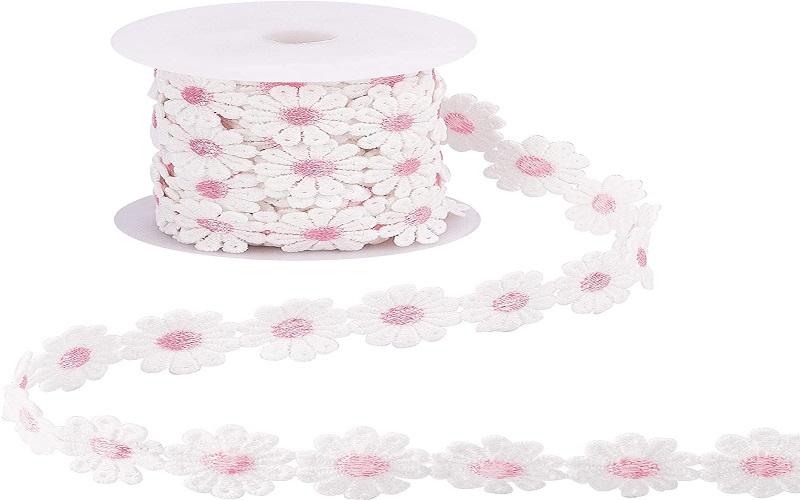
These are just a few examples of plastic spools applications. The versatility of plastic spools means that they can be used for many other purposes as well. The design of a spool (i.e. its size, shape and center hole size) can be customized to its intended use, and this is where plastic bobbin molds come into play.
Advantages of Plastic Spool Mold
In this era of high efficiency and time-saving, plastic wire spool molds have become a popular choice in cable management processes.
Efficiency and Time-saving: Plastic spool produced by injection molding are highly consistent and uniform, making them suitable for automated processes, ensuring smooth and efficient winding and unfolding of cables, saving time during cable production, installation and maintenance. In addition to their consistency, these plastic spools are light and durable, providing excellent protection for the cables inside.
Improve organization:Plastic spools serve as excellent organizational tools that allow cables to be neatly rolled up for easy storage and sorting of different types of cables. This organized storage can significantly simplify the cable management process and make inventory control easier.
Enhance accessibility :With the help of a plastic spool as a tool, cables wrapped around the spool can be easily deployed and retrieved. This simplifies tasks such as installing new cables, performing maintenance on existing cables, or removing old cables.
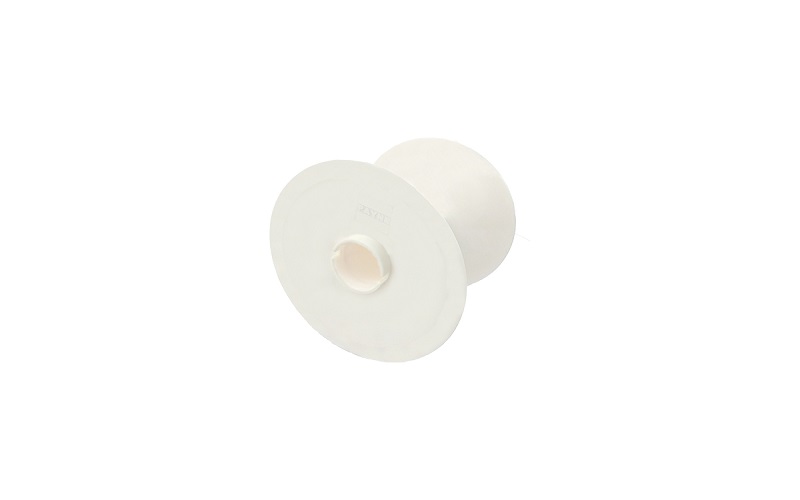
How to Choose Spool Mold Supplier
If you need a plastic spool mold, finding a trustworthy and reliable supplier can be a daunting task. There are several key factors you need to consider before making a decision.
The first step is to look for a supplier that specializes in spool molds and has a good reputation in the industry. Also consider their prices and delivery times, as well as the level of customer service and support they offer. Another important factor is the quality of their products, which can be determined by referring to reviews from previous customers.
FOWMULD has 10 sets of large CNC machining equipment, which can finish the plastic spool molds very well. In addition, we produce 20 pairs of spool molds per year, which can ensure that we have enough production experience.
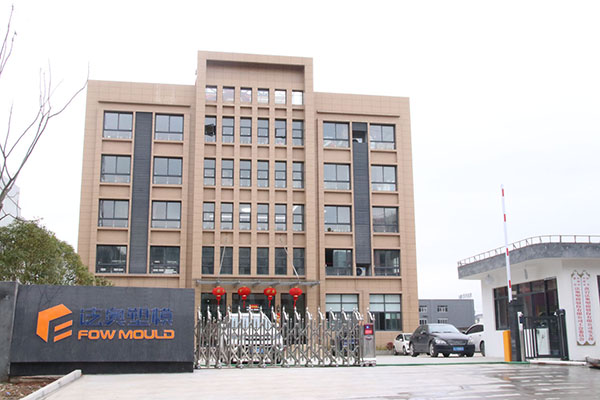