Introduction
Clean, safe drinking water is a basic need for everyone and is usually provided by a water purifier, a device that removes harmful contaminants from water. Plastic purifier mold is specially designed molds used to manufacture various components of water purifiers, such as housings, tanks and filter housings. The precise design of these molds, combined with the efficiency and accuracy of injection molding technology, ensures the production of high quality, reliable water purifiers. In this blog below, you will get a better understanding of how to make high quality plastic filter mold and choose the right water filter manufacturer.
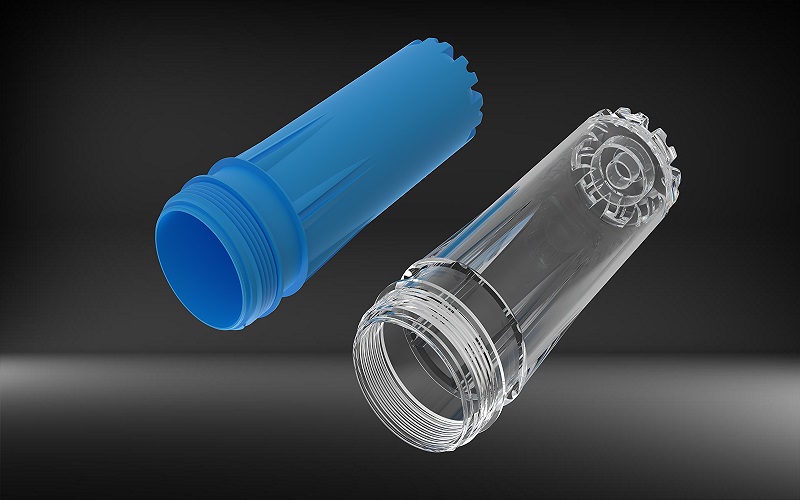
The Design Of Plastic Filter Mold
The design process of these molds often involves careful planning and intricate detailing. Precise measurements and exact specifications ensure the consistency, accuracy, and efficiency of the final product.The design of water purifier molds is a meticulous and detailed process that involves several stages:
First, designers conceptualize the shape, size and function of the parts to be molded understanding the specifications required for each part of the water purifier. This phase also includes planning the design layout, deciding on the materials for the mold, and considering the challenges that may arise during the molding process.
Once the concept is clear, the designer uses CAD (Computer Aided Design) software to create a 3D model of the mold. This model is carefully examined to identify any possible design flaws or improvements. After finalizing the design, a prototype of the mold will be created, used to produce a number of parts, and tested for fit, durability and functionality. During this phase, any necessary adjustments to the design will be made based on the test results.
After prototype testing is completed and all necessary modifications are made, the final mold design is approved for mass production, creating consistent and accurate parts. This meticulous design process ensures the production of quality water purifier molds, which in turn helps create effective and reliable water purifiers.
The Injection Molding Process of Plastic Purifier Mold
Due to the high requirements for efficiency, precision and adaptability of plastic filter molds, injection molding process is usually adopted. The following are the main steps involved in this process:
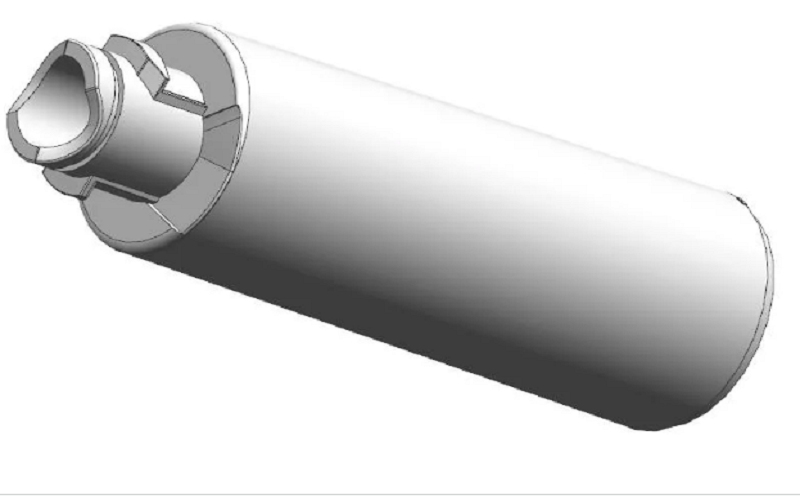
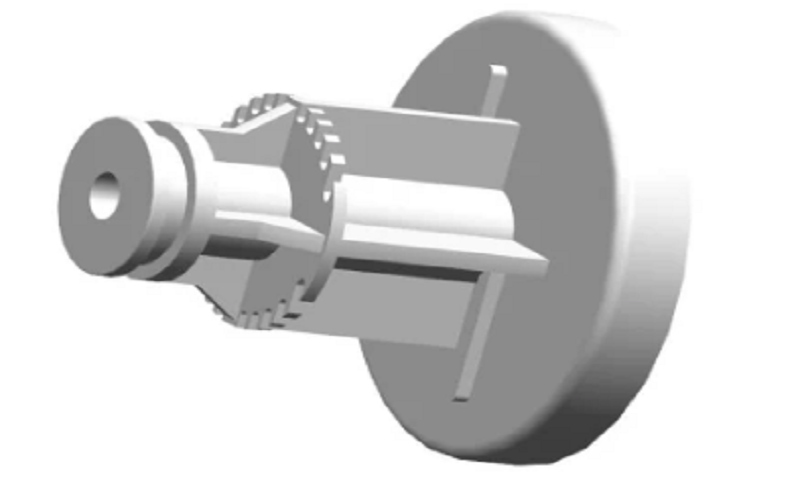
Material Selection and Preparation: The initial stage involves selecting the appropriate material for the component to be molded. Common choices include plastic or metal. The selected material is then fed into the injection molding machine and heated until it reaches a molten state.
Injection:Once the material is ready,the injection unit of a molding machine utilizes a screw to propel the prepared material through a nozzle and fill the mold cavity effectively.
Cooling: Once the mold is filled, the material will go through a cooling phase that allows it to solidify and form the exact shape of the mold cavity. The key point is that the length of the cooling period will depend on the thickness and size of the final product.
Ejection: Once the part has fully cooled and solidified, it is ready for removal from the mold. The mold opens, and the part is ejected using a system of ejector pins.
Post-processing: Lastly, the formed part may go through additional processes such as trimming, painting, or assembly, depending on the design and functionality requirements of the final product.
Common challenges in the manufacturing process
While water filters are essential in our daily lives, the process of manufacturing their molds can be fraught with obstacles. Common challenges faced by manufacturers include the complexity of design, material waste and increased production costs. However, these difficulties should not stop manufacturers from producing high-quality water purifiers.
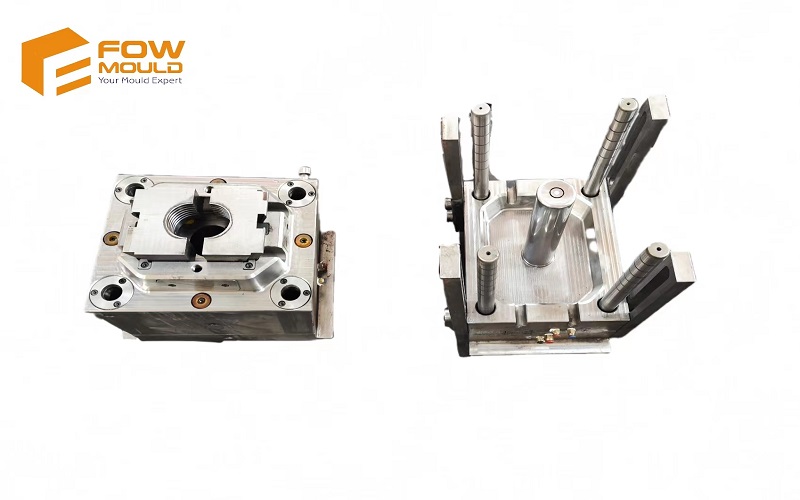
Complex Mould Designs
Water purification equipment is a precision device that often requires complex tooling designs to manufacture various components. These complex designs can be challenging to manufacture and require advanced machinery and skilled labor.Advanced computer-aided design (CAD) software can help simplify the process of creating complex mold designs. Hiring engineers and designers experienced in mold design can also help overcome this challenge.
Material Waste
During the manufacturing process, a large amount of waste is generated, which increases costs and harms the environment. Reducing this waste without affecting the quality of the final product can be a challenge. Strategies to reduce material waste, such as optimizing mold design to minimize excess materials, can help lower costs and make the manufacturing process more environmentally friendly. Reusing or recycling waste can also reduce waste.
High Production Costs
The high costs involved in mold manufacturing are a serious issue. This includes the costs of materials, machinery, labor and energy usage. To address this issue, we can significantly reduce production costs by optimizing operational processes and improving the efficiency of the manufacturing process. Investing in advanced and efficient machinery and equipment can lead to significant cost savings in the long run.
Heat Treatment and Finish Options For Plastic Filter Mold
To ensure the production of high-quality water purifiers, it is important to implement effective heat treatment and finish options for the moulds.Here’s an overview of both processes:
Heat treatment, which involves heating and cooling the moulds to predetermined temperatures, can help improve the durability and strength of the moulds. In this process, the mold is heated to a specific temperature and then rapidly cooled (quenched). This increases the hardness and strength of the mold, but may also make it more brittle. To reduce the brittleness caused by hardening, the mold is then tempered to improve toughness and reduce hardness. In some cases, the mold may undergo annealing, a process in which it is heated and then slowly cooled. This process improves machinability, reduces hardness, and enhances the structural homogeneity of the metal.
Choosing the right finish for a plastic filter mold can improve its functionality and longevity.In this process, a shiny, mirror-like surface is created for the mold. Not only does this improve the appearance of the mold, but it also helps to more easily release the molded part from the mold. In some cases, a texture may be applied to the surface of the mold. This texture will be replicated on parts molded using that mold, giving them a unique look and feel. The mold is then coated with a protective coating that will enhance its resistance to wear, corrosion and heat.
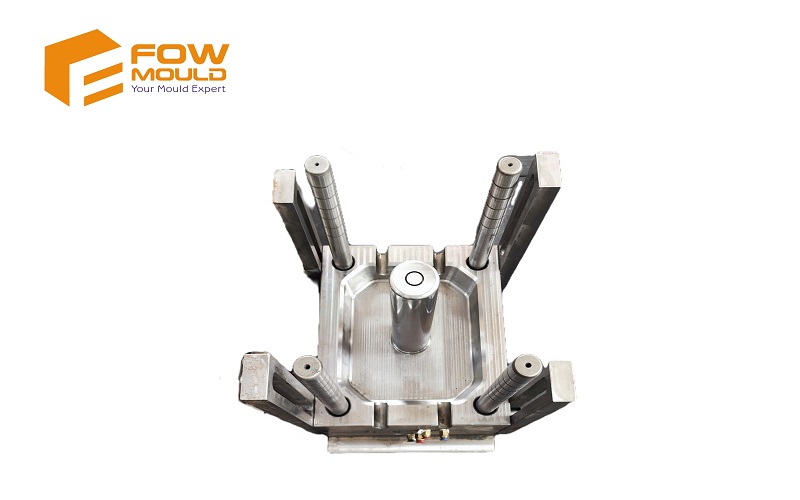
Components Of Plastic Purifier Mold
Plastic filter molds play an important role in forming the various basic components of a water purifier. The following are some of the key components:
Housings
The housing of a water purifier is a critical part of the unit. Its primary function is to protect the internal components of the water purifier, while also providing a sturdy appearance. Given its importance, the quality and longevity of the housing must be of the highest standard to withstand daily wear and tear.
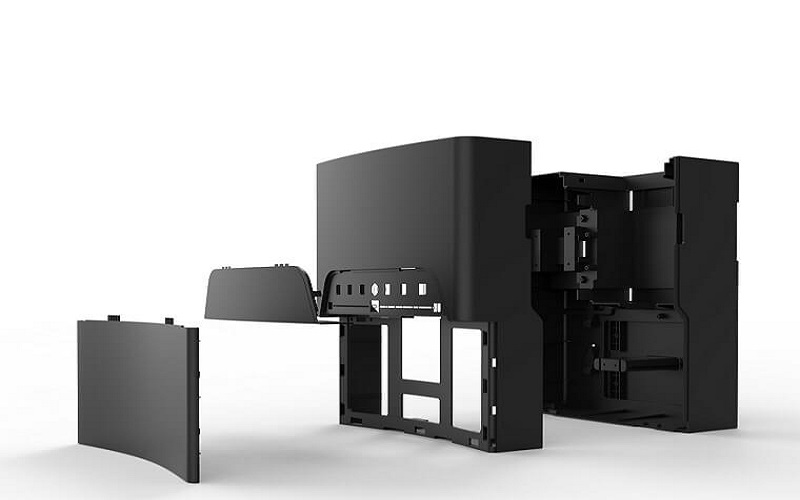
Inner core
The inner core of a water purifier usually contains various filtration media or membranes designed to remove impurities, such as sediment, chemicals, bacteria, and viruses, from the water. It is responsible for the actual purification process by trapping or neutralizing contaminants as the water passes through.
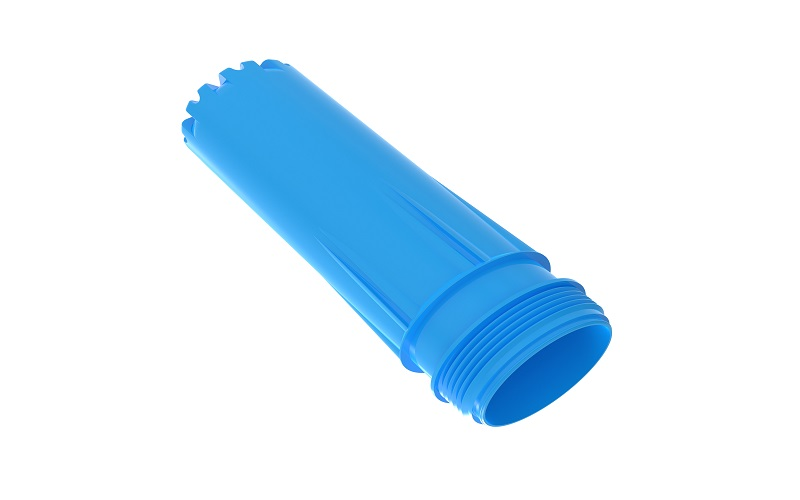
Other Parts
Apart from these, molds are also used to form other integral parts such as valves, knobs, connectors, etc. These parts, although small, play significant roles in the overall functioning of the water purifier.
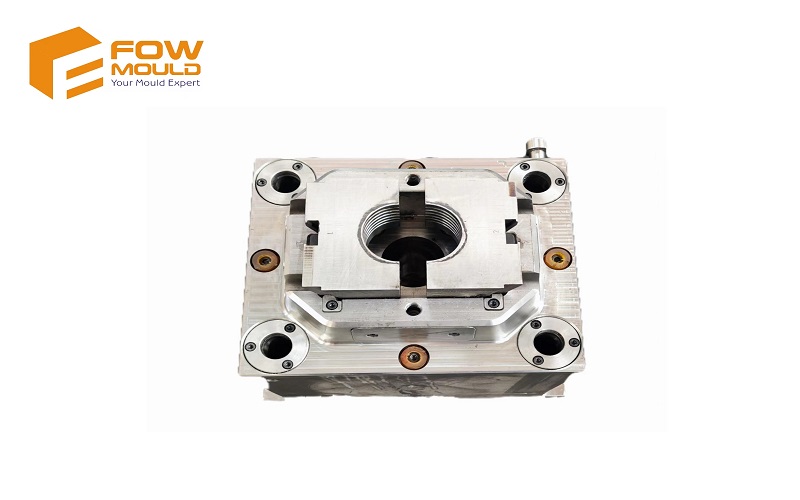
Detailed guide on maintaining plastic purifier mold
Maintaining the moulds used in manufacturing water purifiers is crucial to ensure they continue to produce high-quality components. Here’s a detailed guide on how to maintain these moulds:
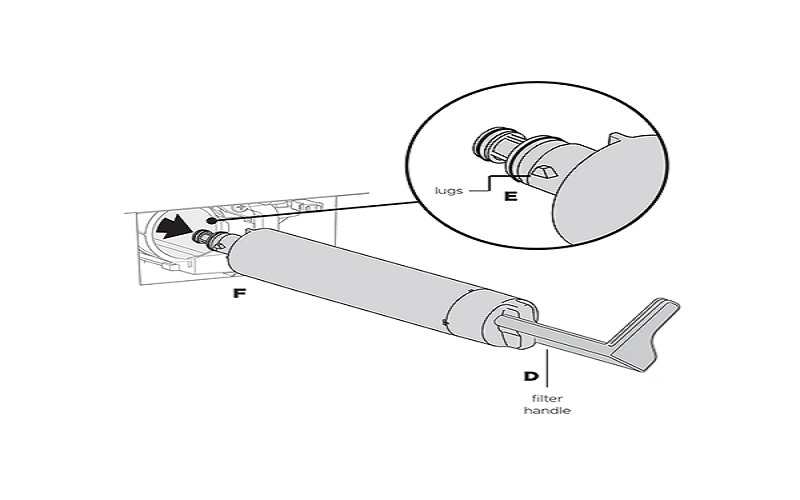
- Regular cleaning and inspection for any signs of wear and tear or damage.Cleaning methods for this process may include the use of solvents or advanced techniques like dry ice blasting and ultrasonic cleaning. In some cases, a simple manual cleaning with a brush can suffice.
- Proper storage conditions to prevent damage and degradation.Moulds should be cleaned, dried, and coated with a rust preventative before storage.The storage area should be dry and climate-controlled to prevent rusting and warping of the moulds.
- Appropriate actions when a mould is found to be defective or damaged.Repair or replace parts promptly when defects or wear are found during inspection. Compatible, high quality replacement parts should be used to maintain mold performance.
How to choose plastic purifier mold supplier in China
In order for a plastic water purifier project to be successful, choosing the right water purifier mold supplier in China is critical to the success of your business, as the quality of the mold will directly affect the quality of your product. The first step is to find a supplier that has extensive experience and expertise in producing water purifier molds. An experienced supplier can provide a high quality product and guide you through the process. Second, put quality over cost and be able to provide durable, accurate, and reliable molds. As a final point, good customer service is critical. The supplier should be responsive to your inquiries, provide clear communication, and offer excellent after-sales service.
As an industry leader in injection molding, fowmould has accumulated a wealth of experience in water purifier mold injection. fowmould has a team of dedicated experts and cutting-edge technology, and has become a reliable partner for companies seeking quality molds for their water purification systems. From design to production to delivery, fowmould strives for excellence in every step of the process. Their commitment to providing top-notch molds is unmatched, making them a trusted name in the industry. Whether you are looking to improve an existing mold or have a new one custom built, fowmould is the ideal choice for all your water purifier mold injection molding needs.
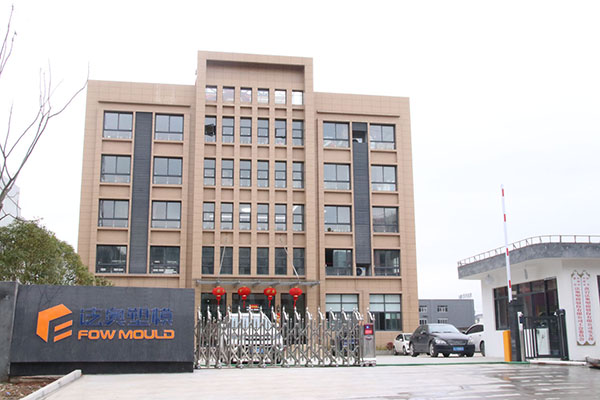
Conclusion
In general, the plastic filter mold manufacturing process involves many steps, starting from design and prototype design to final production. It is necessary to ensure that the quality of the mold meets the required specifications in order to ensure that the final product meets expected standards. In this guide, we have discussed every step of the water purifier mold manufacturing process, including the design and manufacturing process, mold maintenance and repair, and selecting manufacturers. If you want to learn more about water purifier molds, you can consult Fowmould.