As the most produced variety among polyethylene resins, Linear Low-Density Polyethylene (LLDPE) stands out with its exceptional comprehensive properties and extensive applicability. In recent years, the market demand for LLDPE has skyrocketed, leading to a growing interest in the LLDPE injection molding process.
If you’re eager to delve deeper into this process, please continue reading. FOWMOULD will introduce you to the properties and applications of LLDPE, as well as how it is transformed into various products through injection molding technology.
What Is Linear Low Density Polyethylene?
Linear low-density polyethylene (abbreviated LLDPE), usually produced by the copolymerization of ethylene and advanced a-olefins such as butene, hexene or octene at much lower temperatures and pressures.
It is structurally different from regular LLDPE because of the absence of long branched chains.
The LLDPE copolymerization process produces LLDPE polymers with a narrower molecular weight distribution than typical LDPE, and a linear structure that gives them different rheological properties.
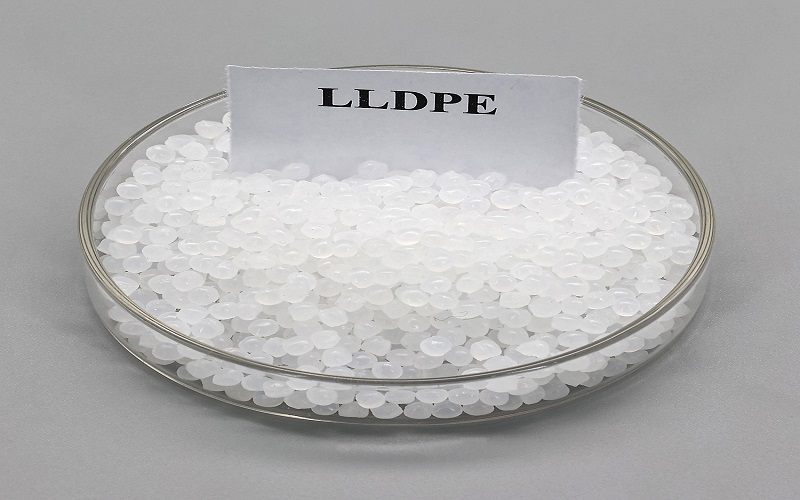
Basic properties of LLDPE plastic
Linear low density polyethylene is non-toxic, tasteless, odorless milky white particles with a density of 0.918~0.935g/cm3.
LLDPE and benzene can dissolve in prolonged contact, and will become brittle in prolonged contact with HCL.
Compared to LDPE material, it has a higher softening temperature and melting point, boasting advantages such as greater strength, good toughness, increased rigidity, excellent heat and cold resistance.
Additionally, it exhibits superior resistance to environmental stress cracking, impressive impact strength, and tear resistance.
It is also resistant to acids, alkalis, and organic solvents, making it widely used in industries such as agriculture, pharmaceuticals, sanitation, and everyday household products.
Comparison of Material Properties between LDPE and LLDPE
Property | LDPE | LLDPE |
Density (g/cm3) | 0.910~0.940 | 0.915~0.935 |
Melting Point (℃) | 105~115 | 110~120 |
Crystallinity (%) | 45~65 | 55~65 |
Mechanical Strength | Relatively poor | High, good toughness, strong rigidity |
Tensile Strength | Low | Higher |
Resistance to Environmental Stress Cracking | Good | Excellent |
What Are The Advantages Of Injection Molded LLDPE?
In modern industrial production and daily life, many plastic products’ processing and production cannot do without LLDPE plastics. The following advantages are reasons why LLDPE plastic injection molding has been successful across various sectors.
Firstly, both LDPE and LLDPE possess excellent rheological or melt flow properties. However, LLDPE has lesser shear sensitivity due to its narrow molecular weight distribution and shorter branches.
Because of its short melt stress relaxation time,injection molded LLDPE have minimal residual stresses, resulting in reduced shrinkage and warpage.
In melt extension, LLDPE typically has a lower viscosity at various strain rates, meaning it won’t strain-harden like LDPE during stretching.
Secondly, LLDPE plastic exhibits outstanding extensibility and significant yield strength, making it easy to mold with superior physical and mechanical properties.
Additionally, rigidity is intrinsically related to density. Thus, the lower the density, the less rigid the material will be, rendering it slightly softer.
For producing soft or high-toughness plastic products, LLDPE plastic is highly suitable.
Lastly, LLDPE plastic can withstand low temperatures, so it’s not prone to becoming brittle, ensuring safety in use and maintaining consistent performance.
It also has a relatively high melting point with favorable heat-sealing temperatures.
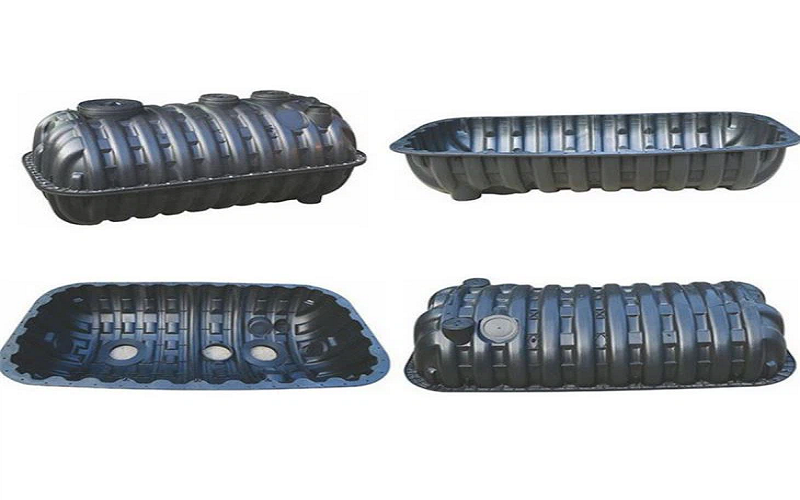
Conditions for LLDPE injection molding
In order to obtain high quality LLDPE plastic products, it is essential to strictly follow the injection molding conditions. The following are important conditions in the LLDPE injection molding process:
Dry Processing
Because LLDPE material is an olefin plastic, it does not absorb water, when producing, no drying is required, but for product quality, it can be dried at a temperature of 60℃ for 1hr to discharge floating water.
Injection temperature
General LLDPE melting point of 170 ° C, decomposition temperature of 300 ° C, injection temperature adjustable range.
Injection molding, the general use of temperature 200 ℃ – 260 ℃, taking into account its apparent viscosity, poor fluidity, a separate LLDPE is difficult to injection molding.
Therefore, it is necessary to increase the power of the injection molding machine or add other low molecular weight plastics to increase its fluidity.
Mold temperature
Generally control the mold temperature in the range of 50-80 ℃, in order to reduce the injection cycle time at the same time and improve the appearance of the quality of the parts.
Injection Pressure
To ensure that the LLDPE material fully fills the mold and to reduce the generation of defects, the injection pressure is usually set at 50-160 MPa.
Runners and Gates
Linear LLDPE has a high melt viscosity, low flow length ratio, lower flowability than LDPE and HDPE, and thin-walled products may lack glue, therefore, the gate and runner are relatively large.
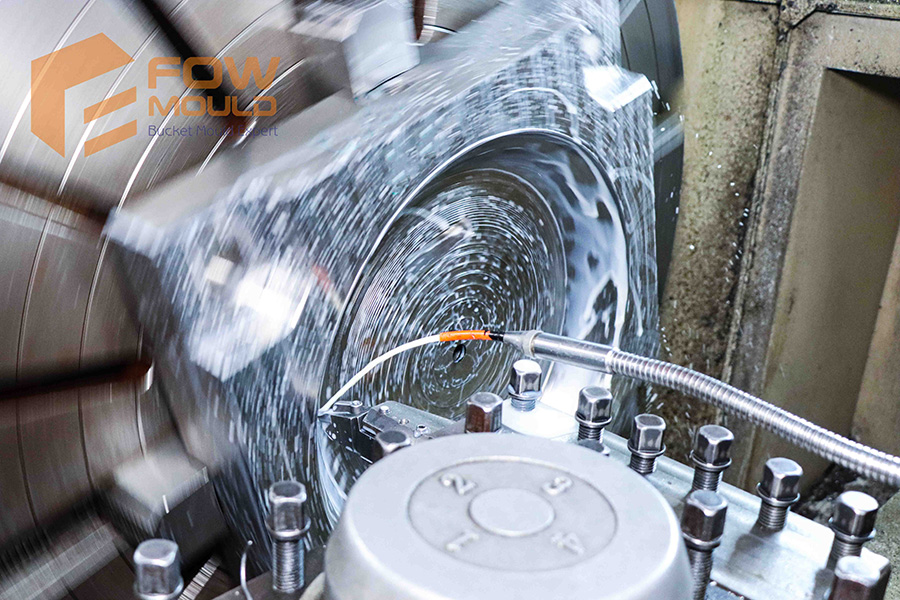
Applications of LLDPE Injection Molding
Injection molding is the primary application market for LLDPE. Due to the high strength of the LLDPE molding , it’s feasible to use high-flow resins, which enhances production efficiency and realizes the thin-walling of LLDPE products, thus making it widely applicable across various domains.
The superior toughness and low-temperature impact strength of this resin make it ideally suited for items such as waste bins, toys, and refrigeration utensils.
Furthermore, LLDPE’s high resistance to environmental stress cracking qualifies it for injection molding caps that come into contact with oily foods, rotomolded waste containers, fuel tanks, and chemical storage tanks.
Its application in pipe linings and wire and cable coatings is smaller, but here LLDPE’s high burst strength and resistance to environmental stress cracking fulfill the necessary requirements.
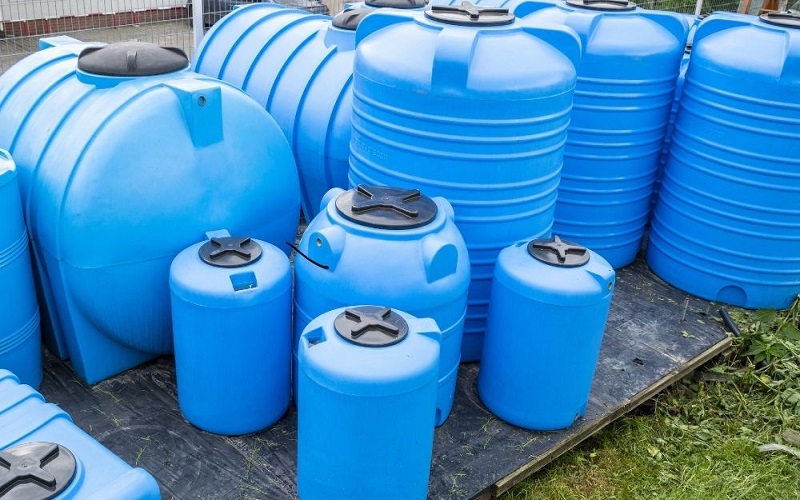
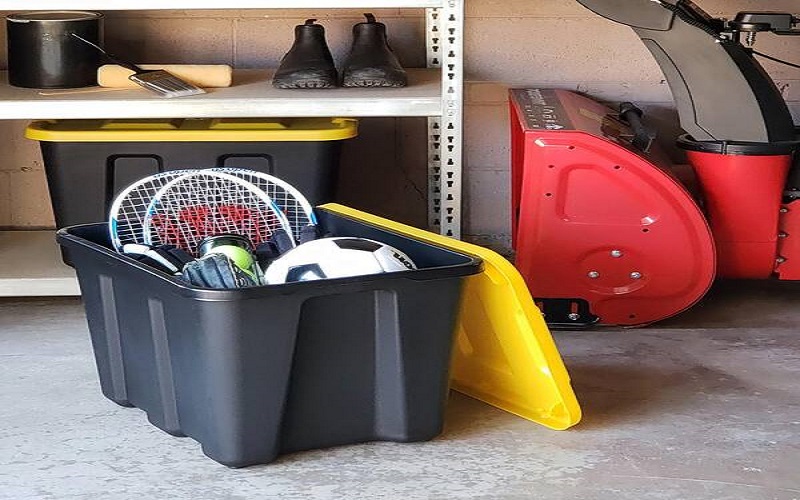
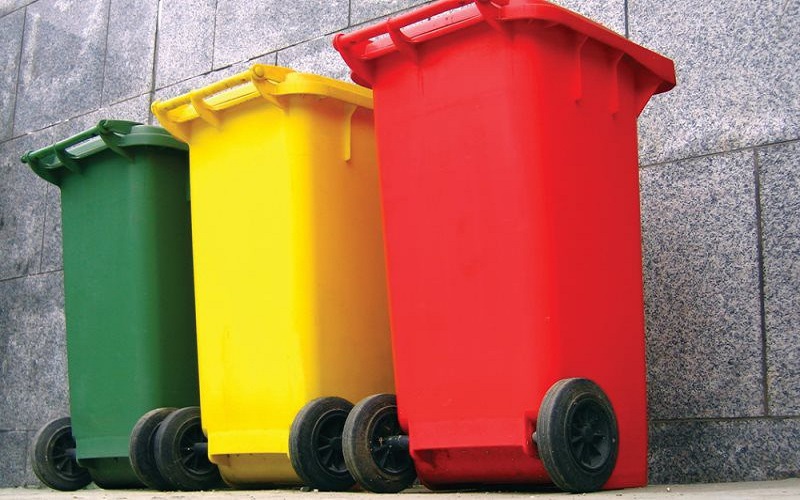
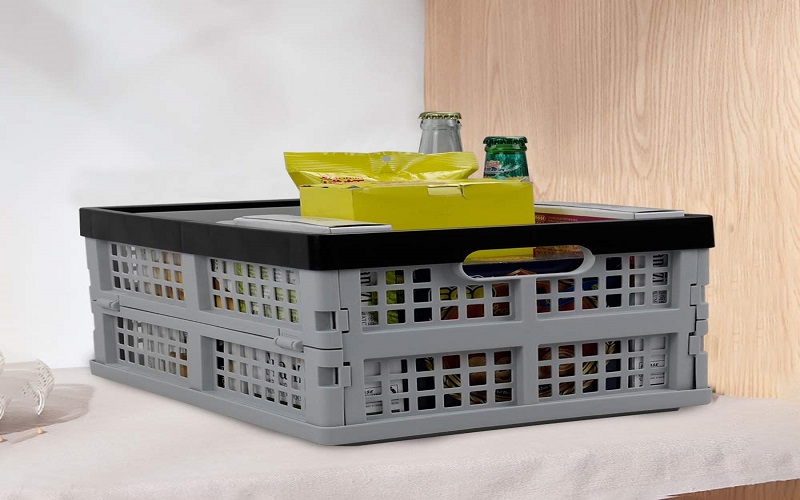
Choose FOWMOULD For LLDPE Injection Molding
If you’re looking to kickstart a new project in Linear Low-Density Polyethylene injection molding, partnering with a reliable and top-tier collaborator is indispensable.
FOWMOULD, with over 40 years of specialization in the injection molding industry, boasts a professional design and manufacturing team. Their profound understanding of the characteristics of each plastic material, combined with an extensive reservoir of knowledge and hands-on experience, continues to fuel FOWMOULD’s relentless advancement.
Furthermore, FOWMOULD offers a one-stop injection molding service, encompassing everything from product design and mold manufacturing to the actual injection molding process. Equipped with the most advanced injection molding machinery in their physical factory, FOWMOULD’s experts constantly monitor the molding procedure, ensuring timely feedback on production details to clients.
Whether it’s PE injection molding, LDPEinjection molding, HDPE modling, or LLDPE injection molding, FOWMOULD will promptly provide you with expert Design for Manufacture (DFM) feedback and offer complimentary quotation services and technical guidance.
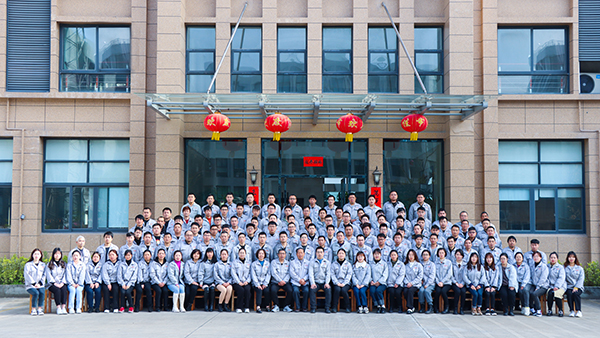