What is Hot Runner Mould?
A hot runner mould is a key player in the world of plastic injection molding. More than a mere buzzword in manufacturing, understanding the concept of a hot runner mould is essential to truly appreciate its revolutionary impact on the molding process.
A hot runner mold is a specially designed injection system, consisting of heated components that keep the plastic in a molten state while it travels from the material hopper to the mold cavities. In contrast to their cold runner counterparts, hot runner moulds offer a streamlined process that ultimately improves production efficiency and reduces plastic waste.
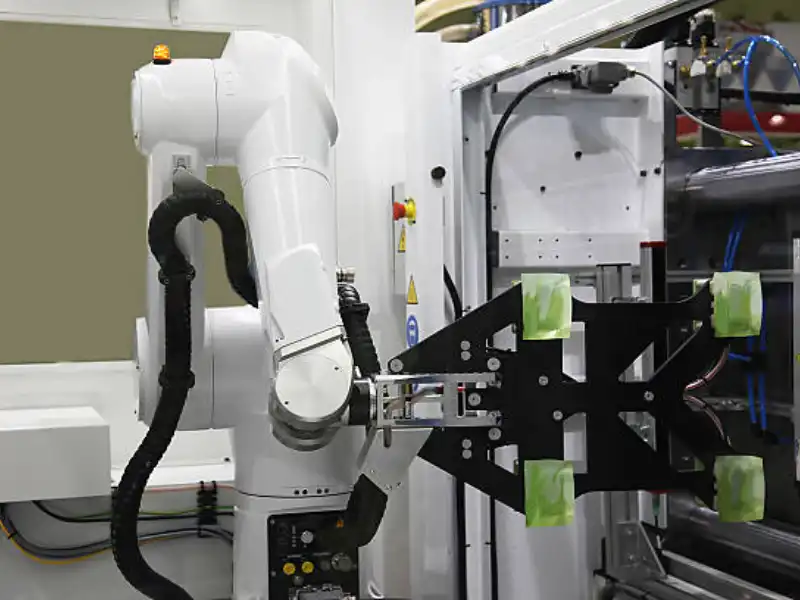
What are the Key Components of a Hot Runner Mould System?
Now, let’s delve deeper into the heart of a hot runner mould system by examining its key components. At its core, a hot runner mould is comprised of two primary elements: the heated manifold and the hot runner nozzle.
The heated manifold is responsible for transporting the molten plastic from the injection molding machine nozzle to the various hot runner nozzles. The temperature controller ensures the manifold maintains a consistent temperature, essential for maintaining the plastic in its molten state.
On the other hand, the hot runner nozzle guides the molten plastic from the heated manifold directly into the cavities of the mold. These nozzles can be designed in different ways, each offering unique benefits and fitting different types of hot runner systems.
What are the Types of Hot Runner Mould Systems?
One glance at the available options, and you’ll see that not all hot runner moulds are created equal. When it comes to types of hot runner systems, you’ll generally encounter three variations: internally heated, externally heated, and insulated runners.
- Internally Heated Systems: These systems heat the thermoplastic resin from the inside, providing even and continuous heat directly. This ensures a smooth run of molten plastic.
- Externally Heated Systems: In contrast to internally heated systems, externally heated systems provide better flow control and uniform temperatures across larger manifolds. This makes them ideal for thermally sensitive polymers.
- Insulated Runner Systems: Despite being simpler, insulated runner systems strike a balance between complexity and performance. They retain heat from the molten plastic rather than supplying external heat, making them an efficient choice for certain applications.
Why choose Hot Runner Moulds?
Hot runner moulds have gained popularity in the plastic injection molding industry primarily due to their numerous advantages. Let’s elaborate on these advantages by looking at specific aspects of the hot runner mould system.
The Role of Temperature Control in Hot Runner Mould Systems
Temperature control plays a pivotal role in maintaining the efficiency and quality of hot runner mould systems. Distinct from their cold runner counterparts, hot runner moulds need to keep the polymer in a consistently molten state during the molding process.
This is achieved through precise temperature controller units, which not only ensure continuous material flow but also preserve the resin’s physical properties. This smooth flow of the molten thermoplastic reduces the chances of material solidification within the runners, leading to fewer blockages and lower maintenance needs.
How Hot Runner Mould Enhances Molding Efficiency
With hot runner mould systems, efficiency is the name of the game. No runner scrap material is produced in a hot runner mold directly related to molding efficiency.
Unlike the more traditional cold runner moulds, hot runners carry the raw material directly from the injection molding machine’s nozzle to the mold cavity, with no need for intermediate cooling. This direct path means less plastic waste, faster mold cycles, and increases molding efficiency overall.
The Impact of Hot Runner Mould on Material Waste Reduction
Reducing plastic waste is not just good economics—it’s also essential for sustainable manufacturing practices. In a world increasingly aware of its environmental footprint, the hot runner’s ability to dramatically reduce plastic waste is a game-changer.
In a hot runner mould, the molten plastic flows directly from the heated manifold to the mold cavities, eliminating the leftover runner waste that would commonly be produced in a cold runner mold. This significant reduction in plastic waste not only saves raw materials but also leads to less post-molding labor and cleanup.
Hot Runner Mould and Faster Injection Molding Cycle Times
When it comes to injection molding, every second counts. Hot runner systems combine speed and efficiency, significantly reducing the cycle time of each injection molding process. How so? Well, unlike cold runner systems, hot runner molds eliminate the need for plastic to cool and solidify in the runners.
This improved efficiency reflects in the faster cooling of the molded part, leading to a shorter overall molding cycle. Plus, the use of hot runners not only makes the molding process faster but also more cost-effective in the long run, especially for high volume production runs.
Improving Part Quality with Hot Runner Mould Systems
Quality is especially crucial with the parts produced through injection molding. The consistent and precise temperature control of hot runner mould systems gives them an edge here. Hot runner technology aids in minimizing the risk of parts being malformed due to cold spots, ensuring the molten thermoplastic fills the mold cavities uniformly.
The result? The high-quality, more intricate plastic parts undergo less stress while being produced. This reduction in stress is attributed to the fact that in hot runner molds, the plastic material is kept in a controlled molten state, eliminating the possibility of premature cooling and hence, ensuring better quality molding.
The Flexibility of Gate Location Design in Hot Runner Mould
Hot runner systems offer great flexibility in gate location design, a feature that comes in handy when molding complex parts. Since the plastic is kept in a molten state, it can be directed into different cavities in the mold simultaneously. This means that the gate locations can be diversified, allowing for the molding of intricate and detailed designs with ease.
As we reach the halfway point of this comprehensive introduction, we can appreciate how hot runner moulds bring increased efficiency, control, and quality to the injection molding process. Stay tuned as we delve into the challenges these systems may present, and how to address them.
How to Deal With the Disadvantages of Hot Runner Mould?
While hot runner moulds offer numerous benefits, they also come with their own set of challenges. Let’s explore these disadvantages and discuss how to effectively deal with them.
The Costs and Maintenance of Hot Runner Mould Systems
Hot runner mould systems, while efficient, can be more expensive to purchase and maintain than their cold runner counterparts. The initial investment for these systems can be high due to the complexity of their design and the technology involved.
However, it’s important to consider the long-term savings that hot runner moulds can provide. By reducing cycle times and waste, and improving part quality, hot runner systems can often pay for themselves over time, especially in high volume production runs. Regular maintenance and proper handling can also extend the lifespan of these systems, further improving their cost-effectiveness.
Polymer Thermal Sensitivity in Hot Runner Mould
Thermally sensitive polymers can pose a challenge in hot runner mould systems. These materials can degrade if they’re kept at high temperatures for extended periods, which can lead to issues with part quality and system performance.
To mitigate this, it’s crucial to use precise temperature control systems and to carefully select the type of hot runner system used based on the specific polymer’s properties. Externally heated hot runner systems, for instance, can provide more uniform temperatures and are often a good choice for thermally sensitive materials.
Challenges in Color Changes with Hot Runner Mould Systems
Color changes can be more challenging with hot runner mould systems. Because the plastic remains in a molten state within the system, it can take longer to purge the old color and switch to a new one.
However, this challenge can be managed with careful planning and the use of purging compounds. By minimizing the number of color changes and scheduling production runs intelligently, manufacturers can reduce downtime and maintain efficiency.
Despite these challenges, with the right strategies and understanding, the benefits of hot runner mould systems can far outweigh the disadvantages.
Hot Runner Mould VS Cold Runner Mould
When it comes to choosing between hot runner and cold runner moulds, understanding the key differences can help make the decision easier. Let’s compare these two systems side by side:
Hot Runner Mould | Cold Runner Mould | |
Waste | Minimal to no waste as the plastic remains molten in the runners. | More waste due to the solidification of plastic in the runners. |
Cycle Time | Faster cycle times due to the elimination of cooling and ejection of runners. | Slower cycle times as the runners need to cool and be ejected. |
Cost | Higher initial cost but can be more cost-effective in the long run, especially for high volume runs. | Lower initial cost but can be less cost-effective over time due to waste and slower cycle times. |
Complexity | More complex system requiring precise temperature control. | Simpler system with less precise temperature control requirements. |
Maintenance | Requires more maintenance due to the complexity of the system. | Requires less maintenance due to the simplicity of the system. |
Conclusion
In conclusion, hot runner moulds have revolutionized the plastic injection molding industry. With their ability to reduce waste, shorten cycle times, and produce high-quality parts, they offer significant advantages over traditional cold runner systems. However, they also come with challenges, including higher initial costs and maintenance requirements.
Despite these challenges, with proper understanding and management, hot runner moulds can provide significant long-term benefits, particularly for medium to high volume production runs. As with any technology, the key to success lies in understanding its capabilities and limitations and using it in the right context.
Opt for FOWMould
When it comes to hot runner mould systems, FOWmould stands out as a reliable choice. With years of experience and a commitment to quality and innovation, FOWmould offers a range of hot runner mould solutions designed to meet the diverse needs of the plastic injection molding industry. Whether you’re producing small, intricate parts or large, complex components, FOWmould’s hot runner mould systems can help you achieve your production goals efficiently and effectively.
And there you have it – a comprehensive introduction to hot runner moulds. Whether you’re new to the world of injection molding or looking to optimize your existing processes, understanding the workings of hot runner moulds can be a game-changer.