Hello there! Have you ever stopped to think about how the plastic parts of your everyday items are made? Well, let me introduce you to a revolutionary manufacturing technique that’s been a game-changer in the world of manufacturing: injection moulding. This process, often performed with a machine called an injection molder, has completely transformed the production of plastic parts, making it faster, more efficient, and incredibly precise.
From the buttons on your remote control to the cap of your water bottle, injection moulding is everywhere. It’s a process that’s been refined and perfected over the years, and it’s become an integral part of the manufacturing industry. But what’s even more fascinating is how it works. The injection moulding process involves melting plastic pellets in a heated barrel, injecting the molten plastic into a mold cavity, and then cooling it to create a solidified product. It’s a complex process, but the end result is worth it: high-quality, identical parts produced at a rapid pace.
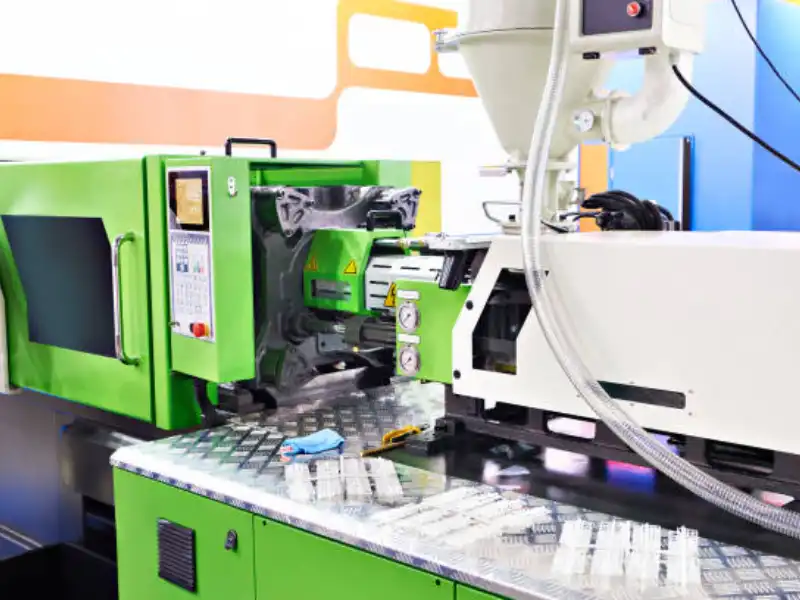
What is Injection Moulding?
So, what exactly is injection moulding? In the simplest terms, it’s a manufacturing process where molten plastic is injected into a mold, then cooled and ejected as a solid part. But let’s break it down a bit more.
First, the plastic material, in the form of granules or pellets, is fed into the injection molding machine through a hopper. The machine has a heated barrel, equipped with heaters and a barrel screw, which melts the plastic. This molten plastic, or resin, is then forced into the mold cavities through the injection unit.
The mold, which is typically made of steel or aluminium, has been designed and machined to the exact shape of the final part. It’s a crucial part of the process, as it determines the shape and size of the final product. The mold is kept at a specific mold temperature to ensure the plastic cools properly.
Once the molten plastic is in the mold, it begins to cool and solidify, forming the final part. After a dwelling phase, where the entirety of the mold is filled with the complete liquid plastic, the clamping unit opens, and the newly formed plastic part is ejected. Voila! You have a finished plastic part, fresh out of the injection moulding process.
The process might sound simple, but it requires a great deal of precision and control. Every part of the process, from the temperature of the heated plastic to the pressure used in the injection unit, must be carefully managed to ensure a high-quality final part. But when done right, injection moulding can produce a wide range of plastic products with incredible efficiency and accuracy.
What is the Role of Injection Moulding in Manufacturing Industry?
Injection moulding has become a cornerstone in today’s manufacturing industry. Why, you ask? Well, it’s all about efficiency and versatility. This process allows for the production of a vast array of plastic parts, each with its unique shapes and sizes. From tiny components in medical devices to large parts in automotive manufacturing, injection moulding has it covered. But it’s not just about variety. Injection moulding is also about precision. The process allows for the production of identical parts, down to the minutest detail. This precision is crucial in industries where even the smallest deviation can lead to significant problems. Moreover, injection moulding is a highly automated process, which means it can churn out parts at a high speed, making it ideal for mass production. And let’s not forget about cost-effectiveness. Once the mold is designed and the machine is set up, producing additional parts is relatively inexpensive.
The Step-by-Step Guide to the Injection Moulding Process
Now that we’ve covered the basics and importance of injection moulding, let’s dive into the injection moulding process step by step. This guide will take you through each stage of the process, from designing the mold to final quality control.
Remember, each step is crucial and requires careful attention to detail. The quality of the final part depends on the precision and accuracy of each stage. So, whether you’re a seasoned professional or a curious newbie, understanding these steps can help you appreciate the complexity and sophistication of this manufacturing technique.
Step 1: Designing the Mold
Designing the mold is the first and arguably one of the most critical steps in the injection moulding process. This is where the magic begins! The mold, often made from hardened steel, pre-hardened steel, aluminum, or beryllium-copper alloy, is precision-machined to form the features of the desired part.
In this stage, engineers use CAD (Computer-Aided Design) software to create a 3D model of the part. This design isn’t just about the shape and size of the final part, but also about how the molten plastic will flow into the mold (the basics of injection), how it will cool, and how the part will be ejected.
It’s a complex process that requires a deep understanding of the properties of the chosen plastic, the requirements of the final part, and the capabilities of the injection moulding machine. But when done right, a well-designed mold can produce thousands, if not millions, of identical parts.
Step 2: Selecting the Right Thermoplastic
Once the mold design is finalized, it’s time to choose the right material for the part. This isn’t a decision to be taken lightly. The choice of material can significantly impact the properties of the final part, including its strength, flexibility, and resistance to heat and chemicals.
Most commonly, thermoplastics are used in the injection moulding process. These are plastics that become pliable or moldable at a certain elevated temperature and solidify upon cooling. Common thermoplastics include polypropylene, polyethylene, and ABS (Acrylonitrile Butadiene Styrene).
The choice of material depends on the requirements of the final part. For example, if the part needs to be rigid and durable, a material like polypropylene might be chosen. On the other hand, if the part needs to be flexible and impact-resistant, a material like ABS might be more suitable.
Step 3: Machine Setup
With the mold designed and the material chosen, it’s time to set up the injection moulding machine. This involves installing the mold onto the machine and adjusting the settings to ensure the process runs smoothly.
The machine setup includes adjusting the clamping unit to secure the mold, setting the correct temperature for the heated barrel, and calibrating the injection unit to ensure the right amount of pressure is applied. It’s a delicate balancing act that requires a deep understanding of the injection moulding process and the specific requirements of the part being produced.
Step 4: Melting and Molding the Resin
Now, we’re ready for the heart of the injection moulding process: the injection of molten plastic into the mold. The plastic pellets are fed into the hopper of the injection moulding machine where they are heated until they become molten. This molten plastic is then injected into the mold cavity under high pressure.
The injection process is a critical stage in the injection moulding process. It requires precise control over the temperature and pressure to ensure the molten plastic fills the entirety of the mold and captures all the fine details of the part design.
Step 5: Cooling and Solidification
Once the molten plastic has been injected into the mold, it begins to cool and solidify. This cooling process is crucial as it allows the plastic to harden into the shape of the mold, forming the final part.
During this stage, the plastic undergoes a transformation from a hot, flowing material to a solid, rigid part. The cooling rate must be carefully controlled to avoid warping or shrinkage of the part. Once the part has fully solidified, the mold can be opened, ready for the next stage of the process.
Step 6: Ejection of the Part
With the cooling process complete, it’s time for the birth of a new component. The clamping unit of the injection moulding machine opens, and the newly formed part is ejected from the mold. This is done using ejector pins which push the part out of the mold.
Ejection might seem like a simple step, but it’s crucial to get it right. If the part is ejected too forcefully or too soon (before it has fully cooled and solidified), it could be damaged or deformed. On the other hand, if the part sticks to the mold, it could be difficult to remove and slow down the entire process.
Step 7: Inspection and Quality Control
The final step in the injection moulding process is inspection and quality control. Each part is carefully examined to ensure it meets the required specifications and quality standards. This might involve checking the dimensions of the part, examining its surface finish, and testing its mechanical properties.
Quality control is a critical part of the injection moulding process. It ensures that each part produced is up to standard and fit for its intended use. If a part doesn’t pass inspection, it’s a sign that something in the process needs to be adjusted, whether it’s the design of the mold, the settings of the machine, or the choice of material.
Why Injection Moulding is a Preferred Manufacturing Method?
Injection moulding comes with a host of advantages that make it a preferred method for manufacturing plastic parts. Here are some of the key benefits:
Advantages | Description |
High Production Speed | Injection moulding is a fast process that allows for high production rates. |
Precision | It can produce parts with complex shapes and fine details. |
Low Labor Costs | The process is largely automated, reducing labor costs. |
High Repeatability | It can produce identical parts over and over again. |
Wide Range of Materials | A variety of thermoplastics can be used, each offering different properties. |
The Challenges of Injection Moulding
Despite its many advantages, injection moulding isn’t without its challenges. Here are some of the limitations to keep in mind:
Challenges | Description |
High Initial Costs | The cost of designing and producing the mold can be high. |
Limited to Thin-Walled Parts | The process is best suited for parts with relatively thin walls. |
Difficulties with Large Parts | Larger parts can be more challenging to produce due to cooling issues. |
Not Suitable for Short Runs | Due to the high initial costs, the process is less economical for short production runs. |
Conclusion
So, there you have it: the injection moulding process step by step. From the initial design of the mold to the final quality control, each step plays a crucial role in creating a high-quality, precise plastic part. It’s a process that requires a deep understanding of materials, machinery, and manufacturing principles, but the results are well worth it.
Looking ahead, the future of injection moulding is bright. With advancements in materials and technology, the process is becoming even more efficient and versatile. New materials are expanding the possibilities for injection moulded parts, while advancements in machine technology are making the process faster and more precise.
But perhaps the most exciting development is the increasing integration of injection moulding with other manufacturing techniques, like 3D printing. This combination is opening up new possibilities for product design and manufacturing, allowing for even more complex and innovative parts.
In conclusion, injection moulding is a vital part of today’s manufacturing industry. It’s a process that has revolutionized the production of plastic parts, and it’s set to play an even bigger role in the future of manufacturing. Whether you’re a professional in the industry or simply curious about how things are made, understanding the injection moulding process is a fascinating insight into the world of manufacturing.