What Is Injection Molding?
Injection molding is a prevalent manufacturing technique used to produce components from a variety of materials, such as polymers, metals, and glass. The injection molding process begins by melting resin, often in the form of plastic pellets, which is then injected at a high-pressure within a mold cavity. This molten material cools and hardens within the cavity, taking on its shape to produce the final product.
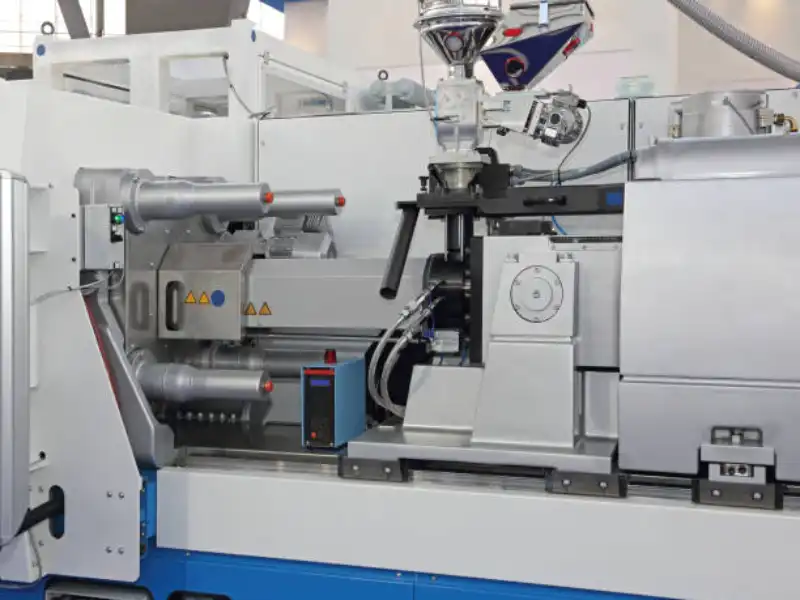
Why Injection Molding Troubleshooting Matters?
Injection molding troubleshooting is an indispensable facet of the production process, holding the significant potential to influence the quality, efficiency, and cost-effectiveness of the output. Harnessing the power of injection molding troubleshooting allows manufacturers to enhance the output quality by mitigating flaws, hence reducing the risk of product returns or recalls, customer dissatisfaction, or worse, safety concerns.
Furthermore, by rectifying the source of errors, manufacturers can streamline the molding process, preventing expensive errors and downtimes, and expediting the production process. It’s worth noting that the implementation of effective troubleshooting can also result in considerable cost savings by minimizing material waste due to defected parts and promoting a more productive use of resources. Hence, injection molding troubleshooting becomes vital to sustain the economic integrity of the business while ensuring the longevity and functionality of the final product.
Types of Injection Molding Defects
Defect | Causes | Solutions |
Flow Lines | Uneven cooling, low injection speed, varying wall thickness | Increase injection speed/pressure, modify mold design |
Burn Marks | Trapped air, overheating resin | Reduce melt/mold temperature, enlarge gas vents/gates |
Warping | Unequal shrinkage during cooling, non-uniform wall thickness | Ensure even cooling, switch to low-shrink material |
Deformation | Improper temperature/pressure regulation | Ensure consistent temperature/pressure throughout the process |
Vacuum Voids | Inadequate molding pressure, premature cooling | Increase injection pressure, manage material properties |
Air Pockets | Improper filling of mold, insufficient pressure or premature cooling | Raise injection speed/pressure, modify mold design |
Sink Marks | Slow cooling of material, insufficient pressure | Increase holding pressure/time, redesign mold for thinner walls |
Weld Lines | Material fronts collide and form weak bonds, premature cooling | Maintain temperature, adjust injection speed/pressure |
Material Discoloration | Long heating time, overly high temperature, contamination | Cleaning injection molding machine, properly manage temperature |
Delamination | Contamination, incompatibility of materials | Ensure resin compatibility, keep inject molding machine clean |
Short Shots | Low injection speed/pressure, insufficient gas venting | Increase injection speed/pressure, improve mold design |
Flash | High pressure or melt temperature, mold wear | Diminish injection pressure, lower melt temperature |
Jetting | Rapid injection speed, small gate sizes | Lower injection speed, enlarge gate size |
Flow Lines
Flow lines are frequent aesthetic defects in injection molding, often manifesting as wavy patterns or discolorations on the surface of the finished molded component. These discrepancies can be unsightly and can adversely affect the overall appeal of consumer products.
Flow lines usually occur due to variations in the cooling speed of the molten material as it navigates through the mold’s cavities, often intensified by differences in wall thickness. Slow injection speed might sometimes result in the material turning partially solid and forming the characteristic wave pattern of flow lines.
Avoidance of flow lines revolves around controlling the temperature, pressure, and rate of plastic injection. Increasing the injection speed, pressure, and the temperature of the material helps ensure that the plastic fills the mold before cooling and reducing the prospect of flow lines. Additionally, making tangible changes to the mold design, like rounding the corners where the wall thickness increases or increasing the nozzle diameter, can help manage flow rates and achieve a more uniform cooling process.
Burn Marks
Burn marks are noticeable defects that surface as black or rust-colored discoloration on the edges or surfaces of the finished product. Generally, they do not affect part integrity, unless the material burn reaches a point of degradation.
The primary culprits behind burn marks are trapped air or overheating of the resin within the mold cavity during injection. Excessive injection speeds or material heating can lead to overheating, resulting in burns.
Burn marks can be effectively prevented by adjusting various parameters of the injection molding process. This involves reducing the melt and mold temperature to avoid overheating, slowing down the injection speed to limit the risk of air trapping inside the mold, enlarging gas vents and gates to allow trapped air to escape the mold, and shortening the mold cycle time to prevent overheating due to trapped air and resin.
Warping
Warping refers to the undesirable distortion that can arise in injection molded products due to the uneven shrinking of different parts of the component. This distortion often results from uneven stresses during the cooling process, resulting in a bent or twisted final product. Factors exacerbating warping include non-uniform wall thickness of the mold, excessively high temperature, or a material with low thermal conductivity.
Preventing warping necessitates a carefully regulated cooling process and mold design. The cooling process should be slow and even, reducing differential stresses on the material. In some instances, it may be beneficial to swap to a material that shrinks less during cooling. One could also redesign the mold to ensure uniform wall thickness and improve stability during cooling.
Deformation
Deformation is another common issue in injection molding, often resulting from inadequately regulated cooling or uneven pressures during the molding process. Deformation can significantly impair the functionality and aesthetic appeal of the finished molded component.
Addressing deformation involves careful regulation of both temperature and pressure within the molding (process). Maintaining a consistent temperature throughout the process, especially during the cooling phase, can help ensure the material contracts at an even rate, lowering deformation risk. Similarly, ensuring consistent pressure during the injection phase helps achieve a more uniform filling of the mold cavities.
Vacuum Voids
Vacuum voids manifest as trapped air bubbles inside the finished molded component, fundamentally a result of inadequate molding pressure. Other factors contributing to this defect could be materials that change density significantly when transitioning from a molten to a solid state or premature cooling of the material closest to the mold wall.
Avoiding vacuum voids necessitates careful regulation of injection pressure and material properties. Increasing the injection pressure helps push out trapped air pockets. Choosing a material with lower viscosity can also reduce the likelihood of air bubble formation. In the case of thick molds, it may be advantageous to place gates near the thickest parts of the mold to prevent premature cooling and void formation.
Air Pockets
Air pockets, similar to vacuum voids, emerge as trapped pockets of air within the finished product, impairing both durability and the aesthetics of the component. The primary cause is improper filling of the mold, arising from insufficient pressure during the injection process or material cooling too quickly next to the mold’s wall.
The prevention of air pockets is primarily achieved by increasing injection speed and pressure, enhancing the mold temperature and design, and ensuring that the material flows properly. One productive strategy is placing the gates closer to the thickest parts of the mold to avert premature cooling, where the material becomes prone to air pockets.
Sink Marks
Sink marks show up as small depressions or indentations on what should be a flat, consistent surface on a molding part. They tend to occur when parts of a component shrink inward, pulling material from outside in, generally due to material cooling too slowly near the part’s exterior.
Overcoming sink marks revolves around adjusting cooling and pressure conditions. This can be done by increasing holding pressure and time, allowing the material near the surface to cool before being absorbed inward or by increasing the cooling time in its entirety to limit overall shrinkage. Redesigning the mold to have thinner component walls can also allow for faster cooling.
Weld Lines
Weld lines appear where the molten material flows in different directions in the mold and then converges again, resulting in weak bonds that reduce the strength of the finished part. This situation typically arises when the fronts of the polymer don’t maintain a certain temperature, become partially solidified upon colliding, and don’t bond sufficiently.
To suppress the formation of weld lines, the material temperature should be increased to prevent partial solidification. The injection speed and pressure need to be elevated to circumvent early cooling of the material before it thoroughly fills the mold. Redesigning the mold to remove partitions and switching to a lower melting temperature or viscosity material can also help.
Material Discoloration
Material discoloration in injection molded products is often due to errors in the choice or preparation of materials, contamination by foreign material, or issues with the molding process itself. Excessive heat or prolonged heating can degrade resin, leading to discoloration of the molten plastic and, ultimately, the final product.
To avoid discoloration, it’s essential to thoroughly clean the injection molding machine between runs, especially when changing colors or types of materials. The temperature settings should be checked frequently to ensure the resin is not heated for too long or at too high a temperature.
Delamination
Delamination occurs when thin layers of the injection molded component peel off from the main structure, appearing similar to a blister. It is typically caused by the presence of foreign material or contaminants (like oil, dust, or rust) in the molten plastic or due to incompatible materials being combined.
Preventing delamination involves ensuring the resin and any additives are compatible and that the injection molding machine and mold are kept clean. It also helps to thoroughly dry the resin before processing, as moisture can also cause delamination.
Short Shots
Short shots represent a condition where the molten plastic fails to fill the mold fully, resulting in incomplete parts. Common causes include incorrect settings for the shot size, injection speed, or pressure; insufficient gas venting, or too thick or complex mold design.
To prevent short shots, the injection speed or pressure may be increased so the mold fills before the plastic has a chance to cool. Improvements in the mold design, such as reducing wall thickness or complexity, or enlarging gas vents and gates, can also alleviate this issue.
Flash
Flash is a phenomenon that occurs when excess molten material escapes the mold cavity and cools, creating unwanted excess around the edges of the product. This can arise from excessive injection pressure, too high melt temperature, or wear and tear in the mold, which leads to gaps.
Mitigating flash involves adjusting process parameters such as lowering the injection pressure and melt temperature. Regular mold maintenance and ensuring a proper clamping force can also prevent flash from happening.
Bubbles
Bubbles are a defect where trapped air or volatiles create voids within the finished product, compromising its aesthetic and structural integrity. Bubbles often occur due to premature cooling near the surface of the part or the presence of moisture in the resin.
Prevention strategies include drying the plastic resin thoroughly before molding, increasing the holding pressure and time to ensure the mold is filled completely, optimizing the cooling process, and venting the mold properly so that gases can escape.
Jetting
Jetting refers to a specific pattern of material wherein the molten polymer does not stick to the mold surface upon injection but is rather dragged along by the filling material, producing snake-like lines. It is primarily caused by a too high injection speed combined with a small gate size, causing the material to “jet” into the mold cavity.
Solutions involve lowering the injection speed so that the material has time to adhere to the mold walls, increasing the size of the gate so the material can flow in a wide front, or changing the gate location to allow the material to spread before reaching the farthest part of the cavity.
Conclusion
Injection mold troubleshooting involves taking stock of the injection molding process as a whole and meticulously identifying the variables contributing to common defects. It demands a careful balance of material selection, processing conditions, and mold design to optimize the part’s functionality and appearance in your injection molding machine troubleshooting endeavor.
Opt for FOWMould
In light of the complexities inherent within the injection molding process, seeking professional assistance to guide and execute productive injection molding troubleshooting can save you frustration, time, and money. FOWMould, as a proven authority in this domain, provides a comprehensive array of injection molding services, including state-of-the-art injection molding troubleshooting solutions. Harness the expertise of FOWMould today to elevate the quality and efficiency of your operations and prevent costly mistakes in your production process.