Introduction
Thermoplastic polyethylene (TPE) mold, also known as thermoplastic elastomer mold, have swept the manufacturing industry. Due to Thermoplastic elastomers (TPEs) have a combination of rubber-like and plastic-like properties, which result in several specific material properties, they have become the preferred choice of many manufacturers in a variety of sectors. Whether it’s automotive parts, toys, medical devices, or hygiene products, TPE molds have proven their worth and gained tremendous popularity. But what sets TPE molds apart from other molding technologies? In this blog, we’ll delve into the world of TPE molds, uncover their secrets, and explore the specific reasons behind their widespread adoption in the manufacturing industry.
The key points of designing a TPE Mould
When designing and manufacturing TPE molds for various applications, it is critical to consider specific design requirements to ensure optimal performance and durability of the TPE product. Therefore, steel reinforcement is strategically incorporated into the design and fabrication of the mold to enhance the mold structure’s ability to withstand heavy use without deformation or damage.
In addition, depending on the specific design requirements of the product, the mold design should consider and increase or decrease the reasonable depth of release with appropriate anti-deformation treatment; also, determine the appropriate TPE product release draft angle to facilitate the release process and reduce the risk of deformation or damage to the product during the release process.
Optimize rib design by adding a reasonable number and size of ribs to provide additional support and minimize bending or deformation. And integrate rounded corners into the mold design to help distribute stress more evenly and reduce the possibility of corner breakage or deformation, while ensuring smooth demolding.
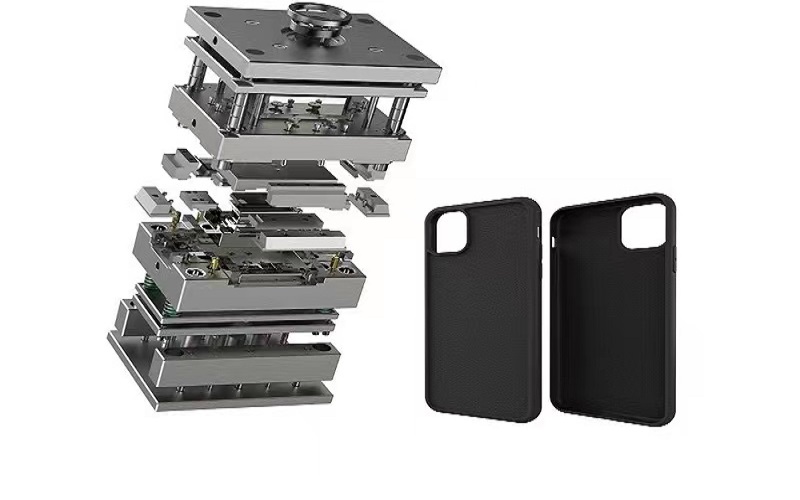
Moldflow of Plastic TPE Mould
Mold flow analysis is an important tool used for TPE mold design and optimization. It analyzes TPE product filling, cooling, warpage, gate and runner design, material selection and design optimization to simulate the injection molding process to predict and analyze the flow behavior of the thermoplastic polyethylene material within the mold cavity. By utilizing mold flow analysis in TPE mold design, manufacturers can gain valuable insight into the injection molding process, optimize mold performance, and ensure the production of high-quality TPE products with minimal defects and increased efficiency.
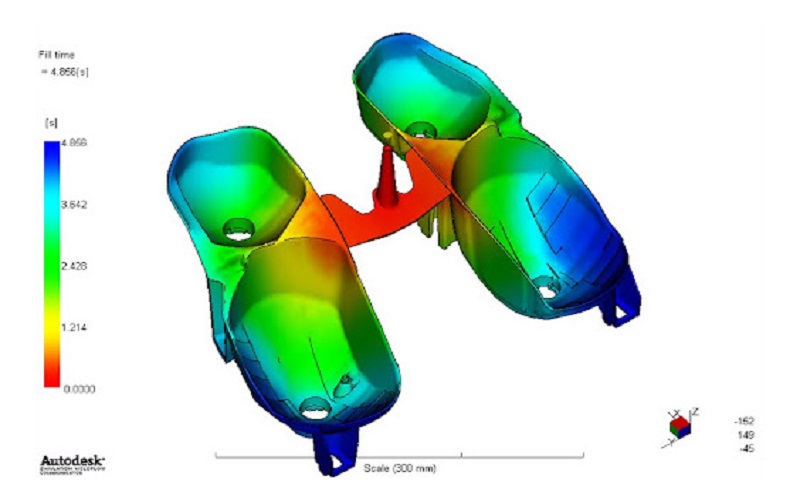
Runner System Of Plastic TPE Mould
TPE molds are often made with cold runner systems. TPE materials are processed at low temperatures and cold runner systems help minimize material degradation. Maintaining the runner size appropriate to the viscosity and flow characteristics of the TPE material used and providing sufficient cross-sectional area to accommodate the desired flow of the TPE material balances the material flow and pressure drop. The design of gates usually selects edge gates, fan gates or direct gates to minimize material waste and improve the cost effectiveness and sustainability of the TPE molding process by optimizing the flow path system.
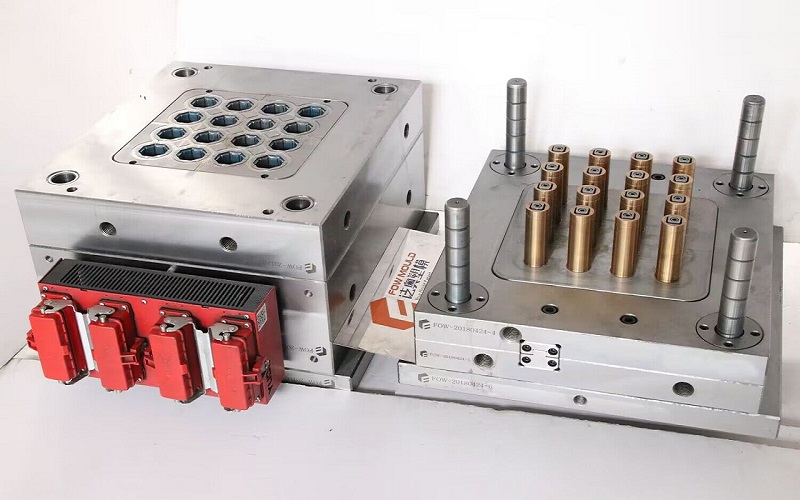
The Ejector System Of TPE Mould
The ejector system of the TPE mold is carefully designed and set up to ensure that the TPE parts are removed from the mold cavity in an efficient and damage-free manner. Accurately positioned ejector pins are used to push the TPE part out of the mold cavity. Depending on the complexity of the TPE part or mold design, additional ejector mechanisms such as stripper plates, air ejectors or mechanical sliders may be used to aid in the removal of TPE parts with recesses or complex features. By taking these factors into account and ensuring a well-designed ejector system, manufacturers can achieve efficient, damage-free ejection of TPE parts from the mold cavity, resulting in high-quality TPE products and a smooth production process.
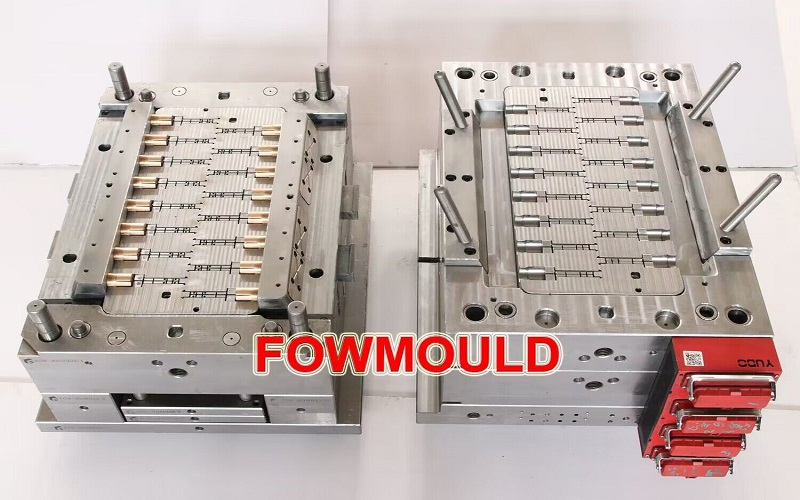
Cooling System Of TPE Mould
Cooling systems are an important part of TPE mold production. A well-designed cooling channel is essential for sufficient cooling time to allow the TPE material to solidify and remain dimensionally stable prior to injection. To ensure smooth processing and avoid potential problems, cooling channels should be located as close to the mold cavity as possible to promote efficient heat transfer. They are usually located at the perimeter of the mold, along the core and cavity surfaces, to ensure optimal cooling of the TPE part. By prioritizing the design of an effective cooling system, manufacturers can optimize productivity and ensure high-quality TPE molds.
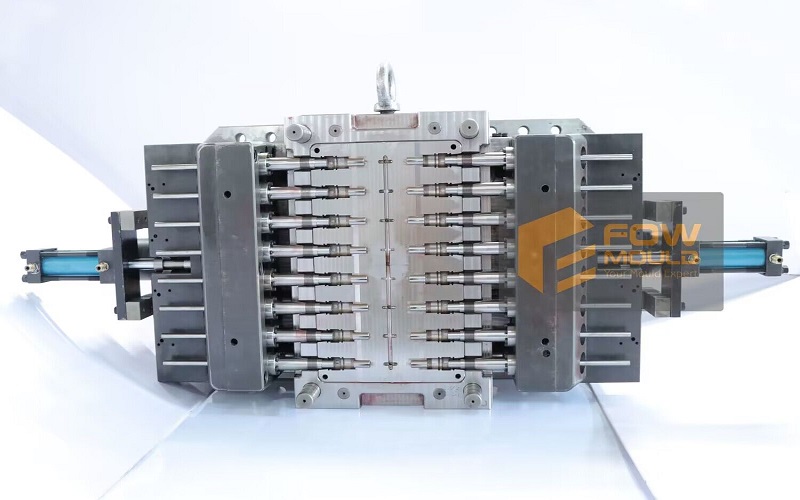
TPE Mold Manufacturing Process
TPE (thermoplastic elastomer) molds are used in the manufacture of goods in a variety of industries, including automotive parts, medical devices and consumer products. Processing TPE molds typically involves several key steps:
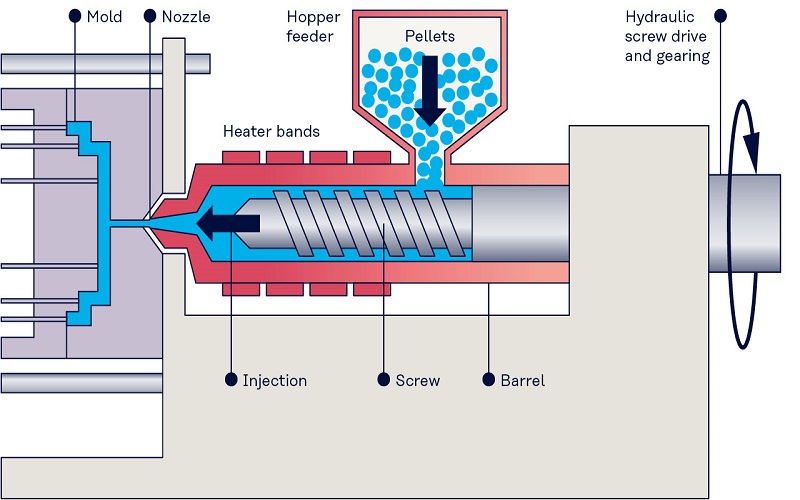
Mold Preparation
Before starting the TPE molding process, the mold must be properly prepared. This critical step includes ensuring that all components, such as the core, cavities, cooling system and ejector system, are in good working condition by thoroughly cleaning and inspecting them. If the mold is not properly prepared, defects or other problems can occur during the molding process, resulting in wasted time, material and money.
TPE Material Preparation
Next, the mold is preheated to the proper temperature to ensure proper flow and adhesion of the TPE material. The temperature level depends on the type of TPE and the desired characteristics of the final product.
TPE Injection Molding
Once the mold is preheated, the TPE material is injected into the mold by a specialized injection molding machine.The TPE is heated to a molten state and then injected into the mold under high pressure to fill the mold cavity. The injection time and pressure are optimized to properly fill the mold cavity without causing defects.
Cooling and Solidification
After the TPE material is injected into the mold, the mold is cooled to the appropriate temperature to solidify the TPE material and ensure it maintains its desired shape. The cooling process can be done with air or water cooling, depending on the type of TPE and the manufacturing requirements.
Ejection
Once the TPE part has sufficiently cooled and solidified, open the mold and initiate the ejection mechanism to remove the part from the mold cavity. This can be achieved through the use of ejector pins, air ejection, or other ejection methods depending on the mold design and part requirements.
Comparison with Liquid Silicone Rubber (LSR)
Thermoplastic elastomers (TPEs) and thermoset elastomers such as liquid silicone rubber (LSR) have different properties and manufacturing processes due to fundamental differences in their structure and behavior.
As noted above, thermoplastic elastomers are processed by heating them above their melting point, shaping them into the desired shape, and then cooling and curing them. The key here is that this process is reversible. If you reheat a molded TPE part, it will return to its original molten state. This property is critical to recycling efforts because it allows TPE parts to be reprocessed and reused.
On the other hand, thermoset elastomers, such as LSRs , undergo chemical changes during their injection molding process. When heated, they cross-link, forming strong chemical bonds that lock the molecules into a rigid structure. This process is irreversible, which means that once a thermoset part is formed, it cannot return to its molten state if reheated. It retains its shape even at high temperatures. This quality is useful for parts that must resist deformation at high temperatures, but it also means that thermoset parts cannot be recycled in the same way as thermoplastics.
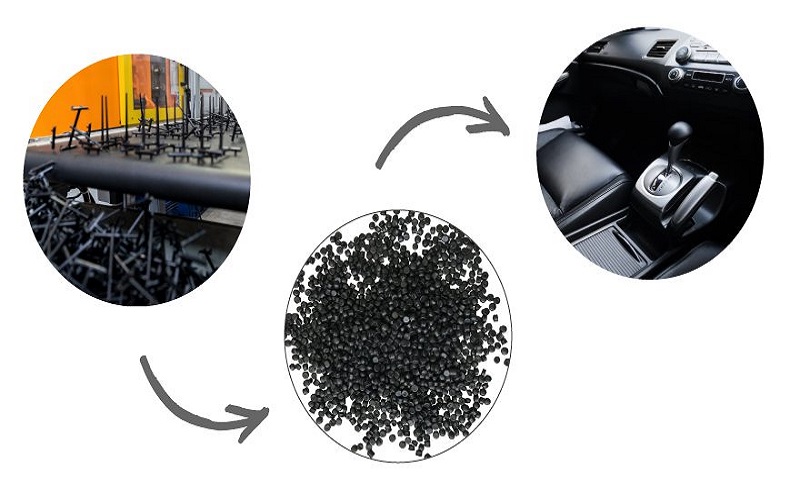
TPE Mould Test
Obtain sample parts from different cavities and batches for mold testing Measure and compare the dimensions of TPE parts to specified tolerances. Use precision measuring tools such as calipers or coordinate measuring machines (CMMs). Inspect for surface defects such as flash, dents, warpage, or other defects. Evaluate physical properties, including hardness, tensile strength, and tear resistance. Conduct functional tests to evaluate performance and durability. Verify compatibility with other parts or substrates. Adjust injection speed, pressure, cooling time, and ejection force to optimize molding cycle parameters. Make adjustments based on test results to refine mold design.
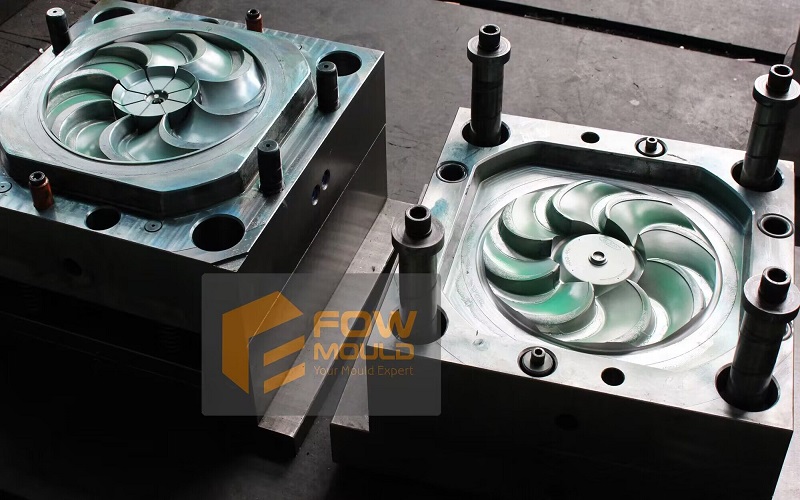
How to Choose TPE Mould Supplier in China
Choosing the right TPE mold supplier is a critical step to ensure the success of your manufacturing business. Since China is known as a center for TPE mold manufacturers, choosing a reliable supplier can be a daunting task.
First, choose a reputable supplier by checking their website, reviews and testimonials from previous customers to get an idea of their reputation. Second, consider the supplier’s production capacity and delivery time. Make sure the supplier has sufficient capacity to meet your production needs and can deliver the molds within the agreed upon deadline. Reliable communication channels and customer service are essential in this regard.
Finally, assess the supplier’s technical capabilities and capacity. Check if they have advanced machinery, skilled technicians and a comprehensive quality control system to produce accurate and high quality TPE molds.
FOWMOULD has 10 sets of large CNC machining equipment, which can do this kind of molds very well.In addition, we make 30 TPE molds per year to ensure we have enough experience.
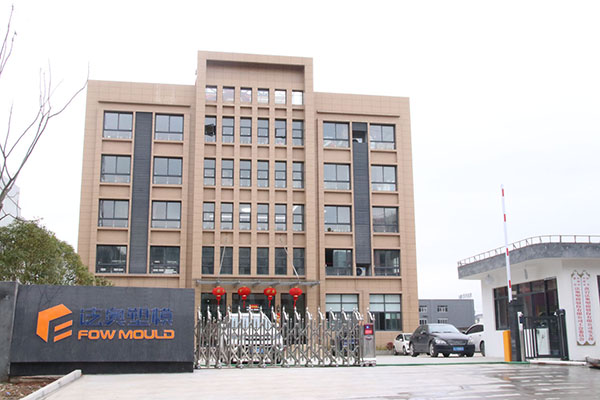
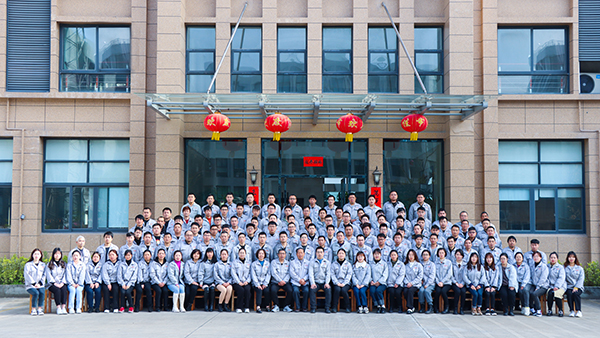