Introduction
Comb mold is specially designed for the production of combs with the unique shape and tooth spacing characteristics of the desired comb design, maintaining quality and consistency throughout the production process.
These molds come in a range of shapes and sizes and can be used for a variety of everyday tasks. From baking to crafting and gardening industries, the ease of use and durability of comb mold make them ideal for those looking to simplify their daily lives.
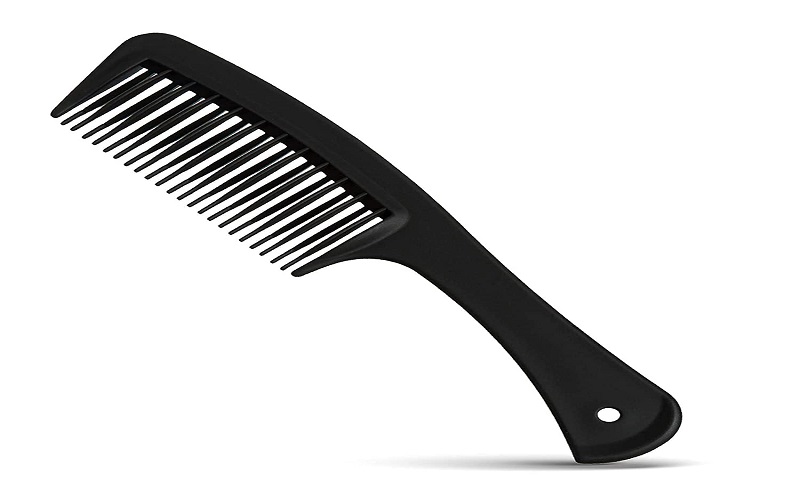
The key points of design for comb mold
When designing a comb mould for manufacturing purposes, several key factors must be taken into consideration to ensure the production of high-quality and functional combs. Here are some of the key points of design:
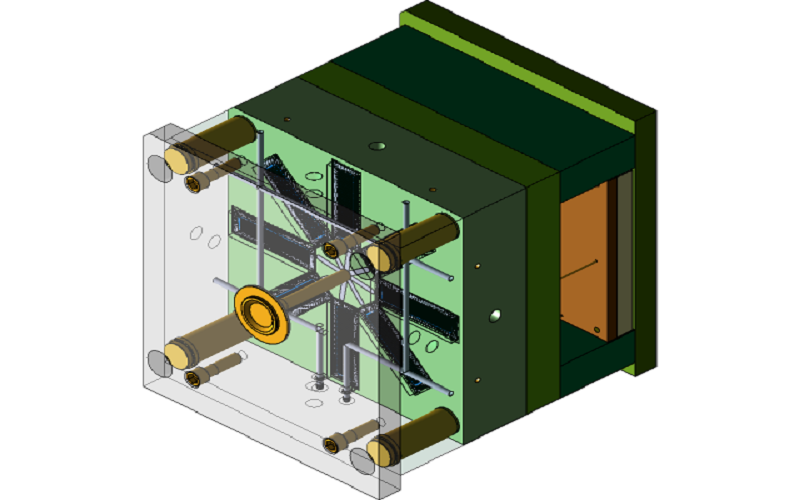
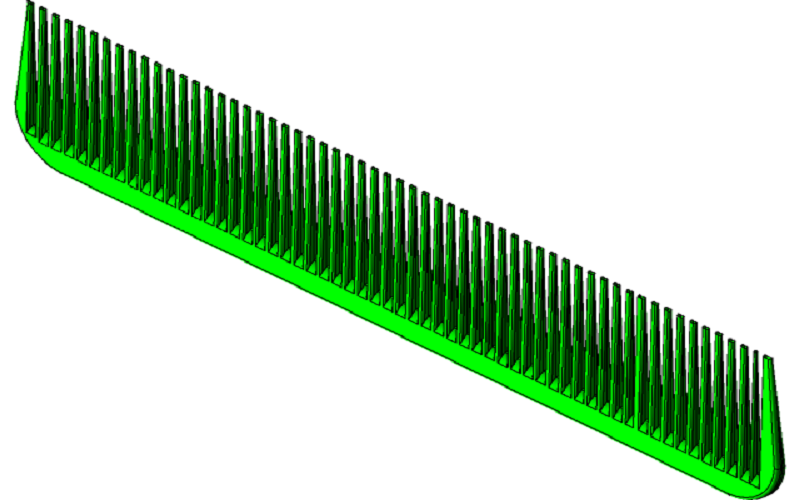
The shape of the comb: The overall shape of the comb is one of the first considerations. It determines the basic form of the mold and affects the user’s handling of the comb. The design should be considered for an ergonomic curved handle design.
Comb tooth design and spacing: Tooth design and spacing are critical in comb mould design. Wider tooth spacing is usually better for combing and thicker hair, while narrower tooth spacing is better for finer hair. The tips of the teeth should also be rounded to prevent scalp injury.
Material Consideration:It is also important to choose the right material. Different materials have different properties when heated and cooled, which must be taken into account. Durable plastic or metal materials, for example, are able to maintain their shape and structure in regular use.
Ease of Production: The comb mould design should facilitate easy and efficient production. The cavities and cores should be designed to minimize the distance the molten material needs to travel. This helps reduce cooling time and potential defects.It should allow for the smooth injection and cooling of the material, and easy removal of the comb once it’s formed.
Aesthetic appearance: Finally, the design of the comb mould should incorporate aesthetic factors to produce a visually appealing comb. The final product should not only be functional, but also have a sophisticated and beautiful appearance.
Details of comb mold manufacturing
There are many complex factors involved in the manufacture of comb moulds, and the following are some important considerations.
First, choose a mold base material with strength, durability, and wear resistance properties, such as hardened steel to make a mold frame that provides structural support and stability throughout the mold assembly. It must be strong enough to withstand the heat and stress involved in the molding process.
The cavities and cores shall be kept smooth during the manufacturing process to prevent sticking of the molding material. Ensure that the cavities and cores accurately reflect the intended design of the comb, including its overall shape, tooth shape and spacing, and any additional features.
Next, make sure the ejector system applies even pressure to the entire comb to prevent damage during the ejection process. Regularly maintain the ejector system to prevent sticking or failure, which can damage the comb mold and product.
After the mold is filled, the plastic is allowed to cool, during which time it solidifies and takes the shape of the mold. The cooling system inside the mold is critical to control the solidification of the molten material and to reduce the number of cycles. Use high quality cooling pipes that are resistant to wear and corrosion to prevent leaks or clogging.
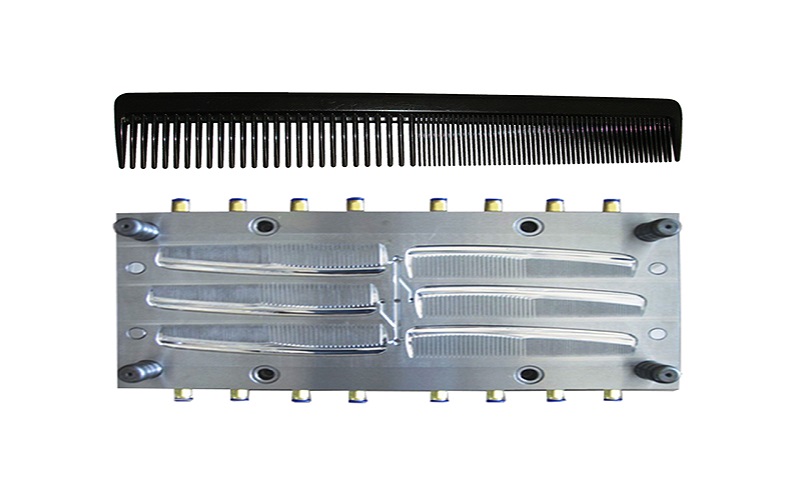
Application of comb mold
Comb moulds are the basic tools used to produce combs, which are widely used as everyday beauty tools in homes, salons and barbershops around the world. Their application spans several fields and contexts:
Demand for Customization
As consumer tastes and preferences evolve, there’s an increasing demand for personalized and unique products. In response, many manufacturers are using custom plastic comb molds to create combs with unique designs, shapes, colors, or even with embedded logos for branding purposes.
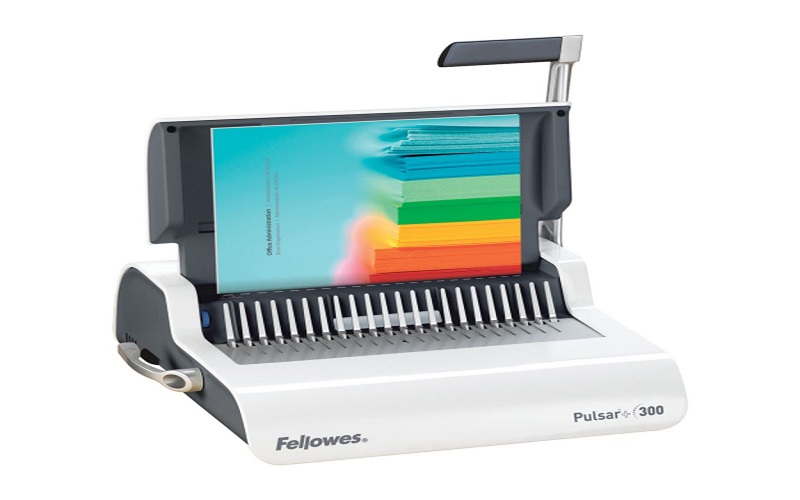
Hairdressing
Combs are also an essential tool for hairdressing professionals. Beauty salons and barber stores require various types of plastic combs, including cutting combs, styling combs and tail combs. These are produced using custom-designed plastic comb molds. For professional hair stylists, comb molds are a boon, allowing custom combs to handle complex hair styles according to the desired style.
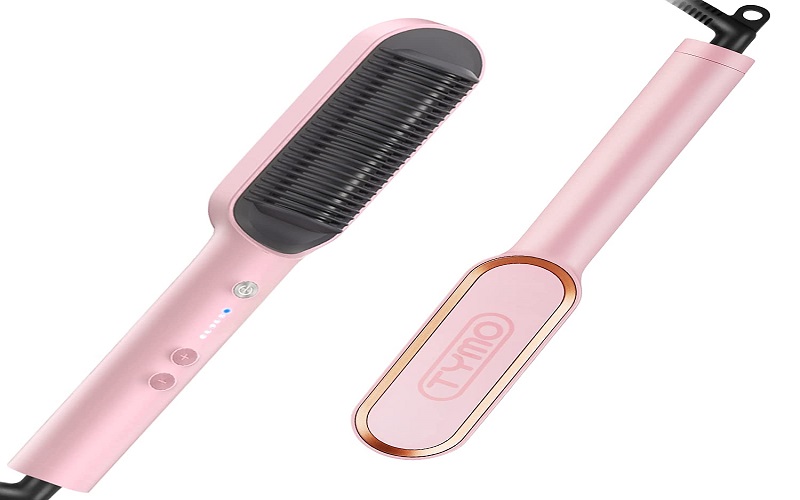
Education and Training
The application of plastic comb mold is becoming more and more popular in educational settings. With the rise of makerspaces and STEM practical education, students are learning manufacturing concepts such as injection molding and prototype design through real-world examples like comb processing. In terms of teaching aids, comb-shaped molds can be used for binding loose-leaf notebooks.
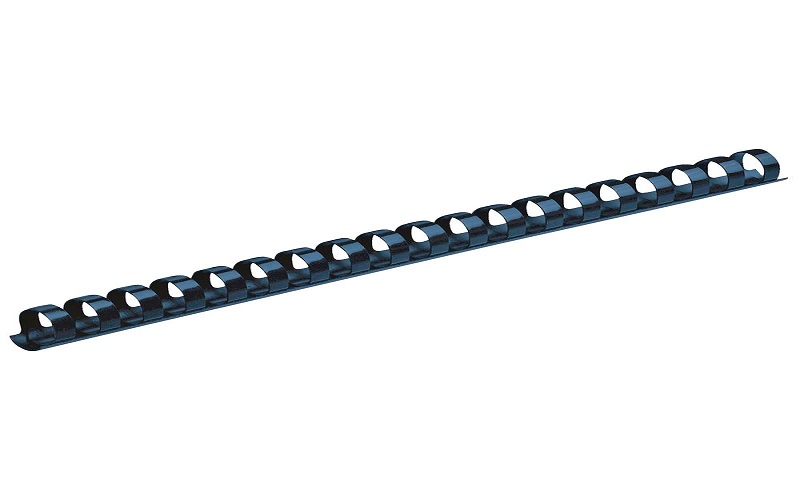
Tips for Cleaning and Maintaining Comb Mold
At the end of each production cycle, clean the mold to remove any residual material. It is important to note that a mild, non-abrasive cleaning solution and soft cloth are used to prevent damage to the mold surface.
Next, the moving parts of the mold, such as the ejector pin, need to be lubricated regularly to ensure smooth operation and prevent premature wear.
Periodically inspecting the mold for signs of wear or damage is an important task. Look for signs of wear, such as scratches, dents, or cracks in the mold surface. Check the alignment and fit of the two mold halves, the condition of the cavities and cores, and the function of the ejector system.
Lastly,When not in use, store the mold in a dry, dust-free environment to prevent corrosion or contamination. Cover the mold with a protective oil if it’s going to be stored for an extended period.

How to choose a comb mold supplier
When it comes to producing high quality combs, choosing the right tooling supplier is critical.
First, consider the specific needs of your business, including the size and style of comb molds needed, as well as any additional services that may be required (such as design assistance or customization). Then, research the suppliers of interest, paying close attention to their reputation, product quality and level of customer service. Reading online reviews, contacting references, and requesting product samples or quotes can all help you make an informed decision.
FOWmould is a professional mold injection molding company with rich experience in manufacturing comb molds and producing large quantities of comb molds for sale to countries around the world every year. We have set up an efficient management team to provide customized comb molds for our customers.
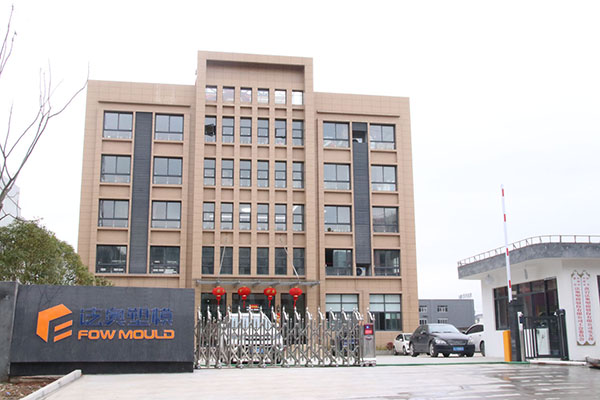
Conculsion
To sum up, comb mold plays a vital role in shaping the final product output, from design to production at every step, and in the future we will push comb tooling forward, opening up new possibilities for custom design and increased efficiency.