Introduction to Moulding Materials for Plastic Injection
In the realm of plastic injection, the selection of moulding materials can significantly influence the outcome of your project. Each material, from the robustness of nylon to the elasticity of thermoplastic polyurethane (TPU), possesses unique properties that can be leveraged for specific applications. But the question is, how do you select the right one? That’s precisely what we’re here to unravel!
Plastic injection moulding is a fascinating world where science and innovation collide, giving birth to an array of products that we use in our everyday lives. From the chair you’re probably sitting on, to the keyboard your fingers are dancing on, injection moulding materials play a crucial role in shaping our world.
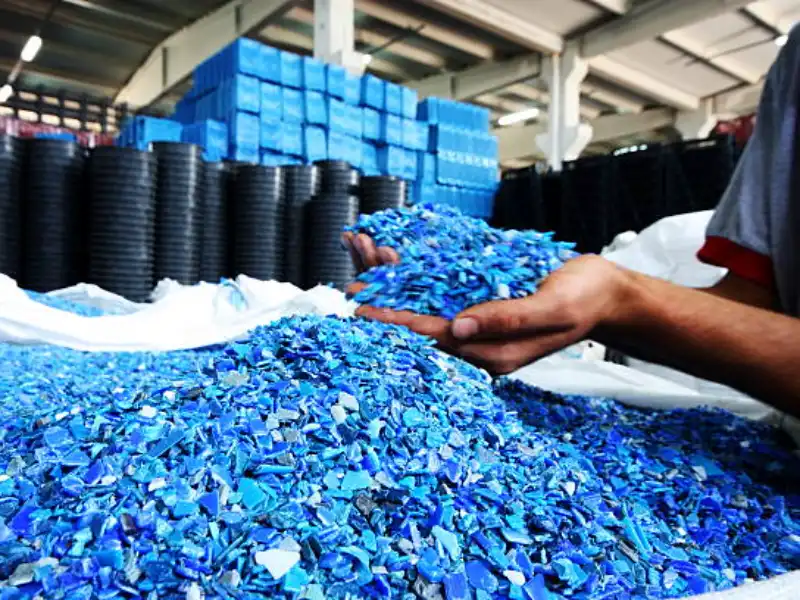
Understanding the Basics of Plastic Injection Moulding
Before we delve into the specifics of moulding materials, let’s take a moment to understand the basics of plastic injection moulding. This process involves melting plastic granules and injecting them into a mould under high pressure. Once cooled, the plastic takes the shape of the mould, creating anything from automotive parts to medical devices. The choice of injection moulding materials can significantly impact the quality, durability, and functionality of the final product.
Plastic injection moulding is a versatile process, accommodating a wide range of materials. The choice of material depends on the product’s intended use, the desired aesthetic, and the production budget. So, without further ado, let’s get acquainted with these materials!
Acrylic (PMMA): A Clear Choice for Moulding Materials
First on our list is Acrylic, also known as Poly(methyl methacrylate) or PMMA. This material is a clear winner when it comes to transparency. Often used as a lightweight, shatter-resistant alternative to glass, acrylic is a popular choice for products requiring clarity and strength.
From display cases to aquariums, and even bulletproof glass, acrylic offers a high degree of transparency while being more impact-resistant than glass. It’s also resistant to UV light and weathering, making it a good choice for outdoor applications. However, it’s worth noting that while acrylic is hard and scratch-resistant, it can crack under extreme force or sudden temperature changes.
Acrylic’s excellent light transmission and clarity make it ideal for optical devices. It’s also used in medical devices due to its biocompatibility. So, whether you’re planning to create eye-catching signage or durable medical equipment, acrylic could be your material of choice!
Acrylonitrile Butadiene Styrene (ABS): Balancing Strength and Aesthetics
Next up, we have Acrylonitrile Butadiene Styrene, or ABS for short. This thermoplastic polymer blends the best of three worlds – the hardness and rigidity of acrylonitrile, the toughness of butadiene, and the heat resistance of styrene.
ABS is a popular choice in the world of injection moulding materials due to its excellent balance of properties. It’s durable, easy to manufacture, and has good dimensional stability. This makes it a common choice for products that need to withstand everyday wear and tear, such as automotive parts, toys, and appliances.
But ABS isn’t just about strength and durability. It’s also aesthetically pleasing, with a natural glossy finish that can be easily colored during the manufacturing process. However, it’s worth noting that while ABS has good chemical resistance, it can be affected by solvents and certain cleaning agents.
So, if you’re looking for a material that offers a balance of strength, aesthetics, and heat resistance, ABS might just be the ticket!
Nylon (Polyamide, PA): The Tough and Heat-Resistant Moulding Material
If toughness and heat resistance are what you’re after, then Nylon, also known as Polyamide (PA), could be your go-to material. This thermoplastic material is renowned for its high tensile strength, impact resistance, and ability to withstand high temperatures.
Nylon is often used in applications where durability and strength are paramount. Think automotive parts, bearings, and gears. It’s also resistant to wear, making it a good choice for moving parts. Plus, its resistance to heat and chemicals makes it suitable for under-the-hood automotive applications and industrial equipment.
However, it’s worth noting that while Nylon is a tough cookie, it does absorb moisture, which can affect its mechanical properties. So, it’s important to consider the environment where your product will be used when choosing Nylon as your moulding material.
Polycarbonate (PC): Combining Strength and Transparency
Moving on, we have Polycarbonate (PC), a strong and transparent thermoplastic material. PC is known for its high impact strength, making it a popular choice for products that need to withstand tough conditions. It’s also transparent, which makes it a great choice for applications that require visibility, such as eyewear and electronic casings.
Polycarbonate also has a high melting point and good thermal expansion properties, making it suitable for products exposed to varying temperatures. However, while PC is a strong and versatile material, it does have poor resistance to scratching and certain chemicals. So, it’s important to consider these factors in your material selection process.
Polyethylene (PE): The Most Commonly Used Moulding Material
Next up is Polyethylene (PE), the most commonly used plastic material in the world. This material is known for its high-density polyethylene (HDPE) variant, which offers excellent rigidity and strength. PE is often used in the production of bottles, containers, and other packaging materials.
PE is also resistant to impact, moisture, and chemicals, making it a versatile choice for a wide range of applications. However, it’s worth noting that while PE is a durable and cost-effective choice, it does have a lower melting point compared to other materials, which may limit its use in high-temperature applications.
Polyoxymethylene (POM): The Engineering Thermoplastic
Also known as Acetal or Polyacetal, Polyoxymethylene (POM) is a high-performance engineering thermoplastic known for its high stiffness and excellent dimensional stability. POM is often used in precision parts that require high stiffness, low friction, and excellent dimensional stability.
POM is also resistant to many solvents and has a low coefficient of friction, making it a good choice for applications like gears, bearings, and fasteners. However, POM is sensitive to UV light and oxidation, so it’s not the best choice for outdoor applications.
Polypropylene (PP): The Versatile and Recyclable Moulding Material
Polypropylene (PP) is a real jack-of-all-trades in the world of moulding materials. This thermoplastic polymer is known for its versatility, offering a balance of chemical resistance, elasticity, and toughness. It’s a popular choice for everything from automotive parts to household goods.
PP is also a champion when it comes to thermal expansion, withstanding temperatures that would make other materials wilt. Plus, it’s resistant to most solvents, making it a good choice for containers and packaging. But perhaps one of the most appealing aspects of PP is its recyclability. In a world increasingly conscious of sustainability, the ability to recycle products at the end of their life is a significant advantage.
However, while PP is a versatile and environmentally friendly choice, it does have a relatively high thermal expansion rate, which can lead to dimensional instability in certain applications.
Polystyrene (PS): Lightweight and Cost-Effective Moulding Material
Next on our list is Polystyrene (PS), a lightweight and cost-effective choice for injection moulding. PS is known for its ease of use and low cost, making it a popular choice for disposable items like cutlery and cups.
PS is also used in higher impact applications, such as casings and housings, thanks to its variant, High Impact Polystyrene (HIPS). However, while PS is a cost-effective and versatile material, it is brittle and can be prone to cracking under stress. It also has poor resistance to UV light and certain chemicals.
Thermoplastic Elastomer (TPE): The Blend of Plastic and Rubber
If you’re looking for a material that offers the best of both worlds, then Thermoplastic Elastomer (TPE) might be the right material for your next project. TPE combines the processing capabilities of thermoplastics with the flexibility and durability of rubber.
TPE is often used in applications that require a soft touch, such as grips, handles, and seals. It’s also used in medical devices due to its biocompatibility. However, while TPE is a versatile and durable material, it does have a lower melting point compared to other materials, which may limit its use in high-temperature applications.
Thermoplastic Polyurethane (TPU): The Elastic and Durable Moulding Material
Thermoplastic Polyurethane (TPU) is a type of elastomer material – a hybrid between hard plastic and soft silicone. A key player in the world of injection moulding, TPU offers a wide range of properties that make it a suitable choice for many applications.
TPU is known for its elasticity and resistance to abrasion, making it a popular choice for products that need to flex or bend without losing their original shape. Think about the protective cases for your smartphone or the soles of your most comfortable shoes – that’s TPU at work!
However, while TPU is a flexible and durable material, it does require precise control over the moulding process to prevent material degradation. So, it’s important to work with an experienced injection moulder when using TPU.
The Role of Resin in Plastic Injection Moulding
Resin plays a crucial role in plastic injection moulding, acting as the base material that is melted and injected into the mould. The type of resin you choose can significantly impact the properties of your final product.
Different resins offer different benefits. Here’s a more comprehensive comparison of some common resins and their key properties:
Resin | Benefits | Drawbacks | Common Applications |
Acrylic (PMMA) | High transparency, UV resistance, good impact strength | Can crack under extreme force or sudden temperature changes | Display cases, signage, optical devices |
ABS | Good balance of properties, easy to mould, good dimensional stability | Can be affected by solvents and certain cleaning agents | Automotive parts, toys, casings |
Nylon (PA) | High strength, heat resistance, and impact resistance | Absorbs moisture which can affect its mechanical properties | Gears, bearings, automotive parts |
Polycarbonate (PC) | High impact strength, transparent, good heat resistance | Poor resistance to scratching and certain chemicals | Eyewear, electronic casings, bulletproof glass |
Polyethylene (PE) | Versatile, high chemical resistance, recyclable | Lower melting point may limit its use in high-temperature applications | Packaging, containers, bottles |
Polyoxymethylene (POM) | High stiffness, excellent dimensional stability, low friction | Sensitive to UV light and oxidation | Precision parts, gears, bearings |
Polypropylene (PP) | Versatile, high chemical resistance, recyclable | High thermal expansion rate can lead to dimensional instability | Automotive parts, household goods, containers |
Polystyrene (PS) | Easy to use, low cost | Brittle, prone to cracking under stress, poor resistance to UV light and certain chemicals | Disposable items, casings, housings |
Thermoplastic Elastomer (TPE) | Combines the processing capabilities of thermoplastics with the flexibility and durability of rubber | Lower melting point may limit its use in high-temperature applications | Grips, handles, seals |
Thermoplastic Polyurethane (TPU) | High elasticity, resistance to abrasion | Requires precise control over the moulding process to prevent material degradation | Protective cases, soles of shoes |
Choosing the right resin for your project is a critical step in the injection moulding process, and it’s important to consider the specific requirements of your product when making your selection.
How Moulding Materials Impact on Product Quality and Durability?
The choice of moulding materials can significantly impact the quality and durability of the final product. Each material has its own set of properties, such as tensile strength, impact resistance, and heat resistance, which can influence how the product performs in its intended application.
For example, a material with high tensile strength and impact resistance, like Nylon, might be a good choice for a product that needs to withstand heavy use or high stress. On the other hand, a material with high heat resistance, like Polycarbonate, might be a better choice for a product that will be exposed to high temperatures.
Here’s a more comprehensive comparison of the key properties of the discussed moulding materials:
Material | Tensile Strength | Impact Resistance | Heat Resistance |
Acrylic (PMMA) | Medium | Low | Medium |
ABS | Medium | Medium | Medium |
Nylon (PA) | High | High | High |
Polycarbonate (PC) | High | High | High |
Polyethylene (PE) | Low | Medium | Low |
Polyoxymethylene (POM) | High | High | High |
Polypropylene (PP) | Medium | High | Medium |
Polystyrene (PS) | Low | Low | Low |
Thermoplastic Elastomer (TPE) | Medium | High | Low |
Thermoplastic Polyurethane (TPU) | High | High | Medium |
Choosing the right material for your product is a critical step in ensuring its quality and durability. It’s important to consider the specific requirements of your product when making your selection.
Environmental Considerations: The Sustainability of Different Moulding Materials
In today’s world, sustainability is more important than ever. When choosing a moulding material, it’s important to consider not only its physical properties and cost but also its environmental impact.
Some materials, like Polypropylene (PP), are recyclable, making them a more sustainable choice. Other materials, like ABS, are not typically recycled due to the difficulty of separating the different components.
Here’s a more comprehensive comparison of the recyclability of the discussed moulding materials:
Material | Recyclability |
Acrylic (PMMA) | Low |
ABS | Low |
Nylon (PA) | Medium |
Polycarbonate (PC) | Low |
Polyethylene (PE) | High |
Polyoxymethylene (POM) | Low |
Polypropylene (PP) | High |
Polystyrene (PS) | Medium |
Thermoplastic Elastomer (TPE) | Low |
Thermoplastic Polyurethane (TPU) | Low |
Choosing a recyclable material can help to reduce the environmental impact of your product. However, it’s also important to consider other factors, such as the energy required to produce and recycle the material, and the potential for pollution during these processes.
Conclusion
Choosing the right moulding material for your project is a complex task. It requires a careful balance of various factors, including the material’s physical properties, cost, ease of use, and environmental impact.
Whether you’re looking for a material with high tensile strength, like Nylon or Polyoxymethylene (POM), or a material with high impact resistance, like Polycarbonate (PC) or Thermoplastic Polyurethane (TPU), there’s a moulding material out there that’s just right for your project.
Remember, the best moulding material for your project is the one that best meets your specific needs. So, take your time, do your research, and don’t be afraid to seek expert advice. After all, the success of your project depends on it!
Opt for FOWMould
At FOWMould, we’re committed to delivering precision and quality in every project. Our in-house manufacturing process allows us to maintain an exceptional level of accuracy, ensuring that your project is handled with the utmost care and expertise.
Our team of seasoned engineers is ready to guide you through the process, providing a comprehensive solution that balances high quality with cost-effectiveness. We’re proud of our commitment to quality, using only top-tier materials for our injection molds and plastic parts.
We’ve established rigorous standards for quality control throughout our production process, from raw material inspection to the final product. This ensures that every part we produce meets our high standards and your expectations.
Ready to elevate your project with FOWMould? Reach out to us today. Let’s bring your vision to life, together!