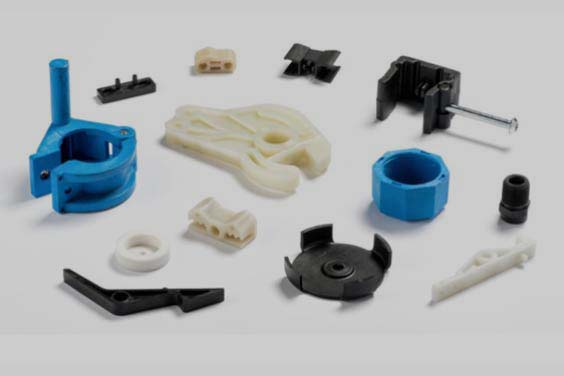
The manufacturing processes involved in the production of plastic and metal materials will differ depending on what you want to achieve. There are different types of processes involved in the production of plastic which may be a bit daunting. This is especially true if you have no idea what the different processes entail. As a business looking to find the best way to manufacture your plastic products, it’s important to learn the basics.
Alternatively, you could rely on qualified mold manufacturers to help guide you on the best processes. Some of the most popular processes are injection molding and casting. They are used by different customers depending on what exactly they want to achieve. Taking a look at injection molding vs casting will give you a better understanding and allow you to implement the right process.
Injection molding is a process used in the manufacture of quality plastic products and features different production stages. It is a reliable and very efficient manufacturing process preferred by most businesses. The defects associated with this method are limited and can easily be fixed to avoid reproducing the same issues.
Additionally, this process features the ability to facilitate the production of multiple products at a go. This helps reduce the time spent in manufacturing and also caters to those looking to get their products in bulk. In this process, there will feature the use of an injection molding machine. This machine is designed to feature all the necessary injection molding machine parts required in the manufacturing process. They include:
Clamping unit
The clamping unit is a handy part that is used to secure the mold to ensure that the molten product introduced finds a steady surface. It features hydraulics that allows it to move in and out facilitating the opening and closing of the mold.
Injection unit
The other important part is the injection unit that is used to introduce molten material into the mold of choice. The injection unit is designed to dwell on the mold to ensure that the molten material introduced is enough. This helps avoid any excess and wastage.
Mold cavity
Perhaps the most important part of this process is the mold cavity. The mold determines the result and should be paid attention to. It should be designed and made to feature the exact features that are required for the product to be manufactured.
When it comes to the process cycle, the manufacturing of these plastic products will feature a few stages. Some of them include:
Product design
The first step is to work on the product design to ensure that you have a clear visual representation of the product you want to be manufactured. This is especially important if you are working with products with intricate details, designs, and complicated shapes. Taking care of this first will give your manufacturers a good base to work off of. Here, you’ll work closely with designers to come up with a mock-up of the product you are aiming for. In this process, you’ll need to include every single aspect you want to be featured on the product.
Mold design
The next thing to consider is the mould design and how the designers will go about it. It is important to ensure that the mold design is accurately catered to. It will determine the outcome of the mold and in turn, the product manufactured. Your designers will work to ensure that they get this right to avoid making any preventable mistakes.
Mold Making
This part of the process is then handed over to qualified engineers who work on the mold and produce a working mold that will be used in the manufacturing process. All the intricate designs featured in the mold design are to be translated into the mold during the mold-making technology.
Injection molding process
Once the mold is done, the injection molding process can then begin with clear guidelines and steps to be followed. The first thing is to introduce the molten material into the mold using the mold. Once this is done, the molten material is left to cool which allows it to take the shape designed in the mold. After the cooling process is done, the end product is released and ejected. Once it is done, you can then get to use the products.
The process is typically faster than casting
Allows for Repeatability
Injection molds feature the use of diverse types of materials
Feature the ability to produce a massive number of plastic products
The injection molding process offers very accurate results, even in high-production
Does not feature high operational costs apart from the initial purchase cost incurred
Injection molds can be quite expensive to create, so tooling budgets will have to be high
The result may be less durable and have a lower quality than one would find in casting
Makes it hard to correct mistakes made
High cost incurred in the initial purchase
Casting is different from injection molding in terms of the processes involved and the material used in the process. The molten material used in this process is mostly metal and is used to manufacture more complex products. These products cannot be manufactured using any other processes. The metals used are the non-ferrous type that includes zinc, tin, copper, and aluminum.
When working with the casting manufacturing method, the mold is lubricated beforehand. This helps regulate the temperature and also makes it easier to eject the product once the manufacturing process is complete. The molten metal material is introduced into the mold with high pressure that continues until the molten material in the mold solidifies. The continuous pressure helps ensure that no part of the molten material solidifies before the casting process begins. Once the product has solidified it is then taken out and can be used in its desired application.
Features great shape tolerances
Helps achieve consistency and uniformity in the design produced
There are no post-casting processes required.
Results in a durable, high-quality product
Casting allows for greater design complexity
It’s ideal for completing many intricate, disparate designs at the same time.
This does not typically allow for the casting of large parts
High melting point metals, like steel, won’t work
Die materials can be expensive
The two methods discussed above feature very significant differences. Learning the differences between die casting and injection molding is essential. It will help you get a better understanding of the two processes. Some of their differences include:
In the injection molding process, the molten material is introduced into the mold using a pressurized injection unit. With die casting, the molten material is simply poured into the mold cavity.
In injection molding, the molds are made using hardened steel while the molds in casting are made using silicone rubber.
Injection molding will feature the use of high-grade plastic products in the molten state while casting will feature us of metals in their molten states.
Injection molding will feature the ability to produce different products in one cycle with the use of multiple mold cavities. However, casting can only work on one product at a time.
When it comes to tooling, the injection molding process will feature higher costs compared to the casting process.
There are different ways to get the product you are in the market for. This goes to show that learning more about the options available to you is essential. Once you have this you can determine which process will work best for you.
Consider working with a molding manufacturer who will guide you and ensure that you get the best plastic injection molding service. The best way to go about this is with the guidance of professionals who have been in the business for years. You’ll get to enjoy the expertise and the peace of mind that the products will meet your specific needs.
Please contact us using the form below or emailing (harry@fowmould.com)