The plastic industry faces a serious challenge today. Landfills are overflowing, marine ecosystems are under threat, and stricter government regulations now target plastic producers and users. Consumers are also pushing back, demanding safer and more responsible manufacturing. These pressures are creating operational and reputational risks for businesses that rely heavily on traditional plastic components.
Injection molding manufacturers now face the difficult task of reducing environmental impact without increasing costs or reducing product quality. Many companies struggle to meet sustainability goals while maintaining high performance and competitive pricing. The need for a smarter and cleaner solution is growing, and timelines are getting shorter.
Biodegradable films may offer the breakthrough the industry needs. These materials provide a path toward cleaner production while meeting strict performance and compliance standards. This article explores how biodegradable films are changing the injection molding process for the better.
Basics of Biodegradable Films
Biodegradable films are plastics that break down naturally through microbes over time. These materials decompose into carbon dioxide, water, and organic matter under specific conditions. Unlike traditional plastics, they don’t persist in landfills or oceans for decades.
Conventional plastics are made from petroleum and resist natural decay. Biodegradable films, however, come from renewable sources and support composting. They reduce long-term plastic waste and lower environmental risks. This makes them suitable for eco-conscious production and packaging.
Common types include PLA (polylactic acid), PHA (polyhydroxyalkanoates), and starch-based blends. PLA comes from fermented plant starch. PHA is produced by bacterial fermentation. Starch films often mix with other materials for better strength. These options offer flexibility, transparency, and strength needed in molding.
Biodegradable films offer a cleaner, adaptable alternative to harmful conventional petroleum-based plastics.
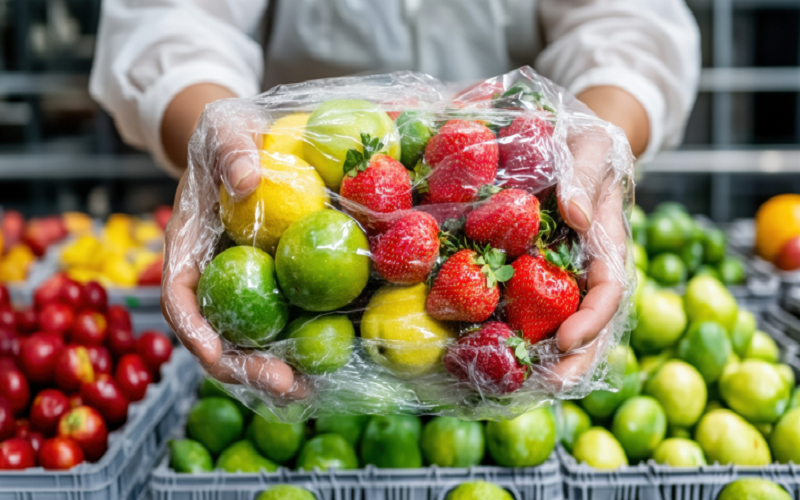
Overcoming Limitations with Next-Gen Solutions
Biodegradable films have limits, especially in shelf-life and storage. Moisture and temperature can degrade them too soon. New treatments now extend their usability and prevent early breakdown.
Coatings and multilayer structures add extra strength and protection. Barrier coatings improve durability without reducing biodegradability. Multilayers allow different features to work together in one product.
Compatibility additives also help. These improve bonding, flow, and flexibility during molding. They allow better integration with standard equipment and boost product performance. To achieve optimal results, you must work with trusted material providers. That includes choosing the right (polyvinyl alcohol) PVA suppliers who offer consistent quality and technical support. Selecting reliable partners ensures material performance aligns with production goals.
Progress depends on collaboration. Material scientists and mold designers must work together. Shared data and testing can speed up product development. Joint efforts can solve molding issues and unlock new design options.
These innovations help biodegradable films meet strict requirements. They make adoption easier and expand use across industries.
Adapting Injection Molding for Biodegradable Inputs
Switching to biodegradable plastic films requires adjustments in molding machines and settings. These materials behave differently than standard plastics and need special handling. Molders must fine-tune their processes to prevent plastic waste and defects.
Biodegradable films are more sensitive to heat, pressure, and moisture. Overheating can damage their structure. High moisture levels can weaken the material before molding. Proper storage and pre-drying help maintain quality and reduce risks.
The processing window is narrower with biodegradable films. You’ll need to monitor cycle times and cooling rates more closely. Minor mistakes can cause cracks, discoloration, or warping. This means more care and control are essential.
The transition often involves a learning curve. Technicians need training. Some machines may need upgrades or new parts. But once set up correctly, biodegradable films can run smoothly and reliably in modern molding systems.
Meeting Sustainability Demands with Bio-Based Films
Bio-based films help manufacturers lower their carbon footprints and reduce landfill waste. They break down faster and cleaner than traditional plastics. Their use supports global efforts to cut greenhouse gas emissions and protect ecosystems.
These films also help companies follow strict environmental rules. Policies like the EU Green Deal and U.S. Plastics Pact promote sustainable materials. Using biodegradable films can make compliance easier and more cost-effective.
There are also strong business incentives. ESG investors favor companies with green practices. Choosing biodegradable films can boost your ESG score. This improves your image and attracts long-term funding.
Green branding creates market appeal. More customers choose products with eco-labels and compostable packaging. Switching to bio-based films positions your brand as responsible and forward-thinking. This can help you stay ahead in a shifting global market.
Improving Product Performance with Advanced Biodegradable Formulations
Modern biodegradable packaging films offer more than just eco-friendliness. New blends now provide greater mechanical strength and flexibility. These materials can match or exceed the durability of standard plastics in many uses.
Manufacturers have also improved heat resistance and barrier properties. Some films now resist higher temperatures and block moisture or oxygen. This makes them useful in the food industry and medical and agricultural applications.
In the medical field, bio-based films work in single-use tools and packaging. They meet hygiene standards while cutting waste. In the food packaging industry, they preserve freshness and extend shelf life. In agriculture, they’re used for mulch films that break down in soil.
These real-world uses prove biodegradable films aren’t just green—they’re also practical. With each upgrade, they become more competitive with traditional plastics in both quality and performance.
Lowering Coss Through Strategic Integration
Many believe compostable films cost too much to use at scale. That’s not always true. Costs are dropping as production grows and more companies enter the market.
Economies of scale help reduce prices. As demand increases, suppliers improve efficiency and cut waste. Material innovation also plays a role. New blends use cheaper inputs and deliver better results with less volume.
Waste reduction adds more savings. Bio-based films can reduce scrap rates when used correctly. This helps cut disposal fees and lowers total production costs.
Hybrid models offer another option. You can mix biodegradable films with recycled plastics. This reduces costs while keeping performance high. These blends meet many green goals without heavy spending. They also help balance quality, price, and sustainability.
Strategic use of these films can make eco-friendly production both practical and affordable.
Scaling Up Without Compromising Efficiency
Several large manufacturers now use biodegradable films in full-scale operations. Packaging, consumer goods, and agriculture sectors lead the way. These companies show that eco-friendly production can meet high-volume demands.
Automation plays a big role in this success. AI systems monitor temperatures, cycles, and pressure in real time. They adjust settings instantly to reduce waste and boost output. This supports smooth integration of biodegradable materials into existing lines.
Continuous production needs careful planning. Bio-based films can be more sensitive to wear and contamination. Regular mold maintenance prevents defects and downtime. Upgrades to cooling and drying systems may also be needed.
With the right tools, manufacturers can scale without losing speed or quality. Adopting smart systems ensures consistent results and long-term cost savings.
Preparing for Regulatory and Consumer Shifts
Laws targeting plastic use are increasing worldwide. Bans and taxes now affect packaging and production choices. Using biodegradable films helps manufacturers stay ahead of these changes and avoid penalties.
Eco-labels and certifications are also growing in importance. Meeting standards like ASTM D6400 or EN 13432 proves a product’s compostability. Passing biodegradability tests builds trust with regulators and buyers.
Consumer awareness is rising. People now expect clear information on disposal. Labels should explain composting rules and end-of-life handling. This reduces confusion and improves product reputation.
Education drives change. When users understand how and where to discard products, adoption rises. Training teams to handle these materials also boosts results.
Planning for these shifts ensures compliance and builds a loyal customer base. It turns regulation into a market advantage.
Enhancing Supply Chain Transparency with Biodegradable Materials
Biodegradable films can improve traceability across your supply chain. These materials often come from renewable sources like corn or sugarcane. Tracking their origin supports full transparency from source to end product. This helps prove sustainability claims to regulators and consumers.
Clear documentation and sourcing data build trust. Buyers want proof that materials are safe, ethical, and eco-friendly. Using biodegradable films allows better tracking of environmental impact at each stage. Supply chain audits become simpler and more accurate.
Digital tools can support this shift. QR codes, blockchain, and smart labels link products to sourcing info. These tools improve accountability and help meet compliance rules. As transparency grows more important, biodegradable films give your supply chain a competitive edge.
Strengthening Brand Loyalty Through Eco-Conscious Practices
Switching to biodegradable films can build stronger relationships with your customers. Today’s buyers support brands that act responsibly. Using eco-friendly materials shows that you care about the planet and future generations.
Loyal customers return when they see real action. Highlight your use of biodegradable films in product labels, ads, and packaging. Clear messaging helps people connect with your values.
This shift can also spark word-of-mouth support. Happy customers share their positive experiences. Your brand becomes known not just for quality but also for responsibility. Over time, this can drive repeat sales and long-term brand growth.
Conclusion
Integrating biodegradable films could shift your entire approach to sustainability. Their use can support cleaner operations, lower emissions, and meet rising consumer expectations. This change could also boost your position in markets where green values drive purchase decisions.
Start by reviewing your current materials and production methods. Find areas where bio-based inputs can replace harmful plastics. Assess packaging, components, or disposable parts. Each change you make can reduce impact and build a stronger brand.
Explore emerging technologies to stay ahead. Partnering with biotech startups can unlock new options. Enzyme-based enhancers speed up film breakdown after disposal. This gives you an edge in both innovation and compliance. Investing in these solutions supports long-term goals and future growth.