In modern manufacturing, injection molding is most widely used methods for producing to create the desired part. With the continuous growth in mass production demands, achieving cost efficiency while ensuring product quality has become a key focus in the industry.
Multi cavity mold, as an efficient mold design solution, have gradually become one of the core technologies in the field of plastic injection molding due to their ability to significantly improve production efficiency and reduce manufacturing costs.
This article will provide an in-depth analysis of the definition, design principles, and advantages of multi-cavity molds, as well as explore their practical applications in injection molding, helping readers gain a comprehensive understanding of this advanced technology and its tremendous value.
What Is Multi Cavity Mold?
Mold include the mold cavity and the mold core, which are tightly combined to form the overall shape and internal structure of the mold . The mold cavity is primarily responsible for forming the product’s internal shape and structure and controlling the product’s precision.
A multi cavity mold is a design that includes multiple cavities within a single mold, allowing multiple same part to be produced simultaneously in a single cycle.
This type of mold is used to manufacture different components of a multi-part assembly, or multiple variations of a single component, in a single shot.
Compared to traditional single cavity molds, multi-cavity molds can produce multiple parts simultaneously in one injection cycle.
This design significantly improves production efficiency and is especially suitable for large-scale production of small to medium-sized plastic parts, such as bottle caps, medical device components, and electronic product housings.

Design Considerations For Multi Cavity Mold
The design of multi cavity molds requires consideration of multiple key factors to ensure a balance between production efficiency and product quality.
They use more complex gate and runner systems, as well as cooling channels. The following are several careful consideration in the design process:
Runner Systems
In multi-cavity injection molds, the runner system is typically designed in an “H” shape. The “H”-shaped runner system is geometrically symmetrical from the injection nozzle to each cavity, which is also known as a “geometrically balanced” or “naturally balanced” runner system design.
Gate Placement
The gate size should be precisely calculated and designed based on the volume and shape of each cavity, as well as the distance from the main runner. For cavities farther from the main runner, the gate size should be appropriately increased to compensate for pressure loss of the plastic material flowing through the runner.
Mould Structure And Parting Surfaces
Considering the high requirements for the appearance quality of plastic parts, general dimensional accuracy, and high assembly precision, the mold adopts a multi-cavity and multi-parting surface design.
The parting surfaces should be selected at the largest contour of the plastic part’s shape to facilitate smooth demolding of the part, and as much as possible, straight parting surfaces should be chosen to simplify machining.
Exhaust System
A good exhaust design can promptly discharge gas inside the cavity, preventing gas accumulation that forms back pressure and affects the filling pressure of the molten plastic.
Exhaust grooves or exhaust inserts can be set at appropriate positions of each cavity to ensure smooth gas discharge, allowing the molten plastic to fill the cavity steadily.
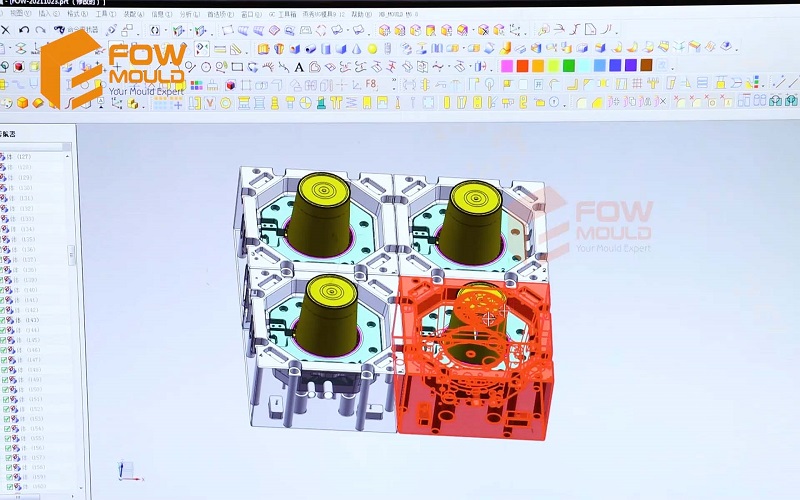
Benefits Of Multi Cavity Injection Molding
The widespread application of multi-cavity molds in injection molding stems from their significant advantages:
Enhance Production Efficiency
Multi-cavity molds produce two or more identical parts from the same mold within the shot guarantee, effectively reducing the overall production cycle time per part.
This leads to a significant boost in production efficiency, making it ideal for manufacturers aiming to meet high production volumes without compromising quality.
Reduced Unit Cost
By producing several parts simultaneously, multi-cavity injection molding reduces the mold cost per part and spreads the energy consumption and labor costs over a larger number of pieces. This substantial cost reduction makes it a preferred choice for large quantities and mass production runs.
Improve Product Accuracy And Consistency
The balanced runner system and uniform material flow ensure that molten plastic fills each cavity evenly, resulting in molded parts that maintain consistent quality and dimensional accuracy. This consistency is crucial for critical parts used in industries like medical devices and electronics.
Increased Adaptability And Flexibility
Multi-cavity molds can be designed as family molds to produce different shapes or components in the same cycle, providing flexibility for complex assemblies and reducing the need for multiple molds. This adaptability supports both large-scale production and low volume production process.
In summary, multi-cavity injection molding offers a perfect mold solution for injection molding manufacturers seeking lower cost per part, higher molding efficiency, and consistent quality, making it a cornerstone technology in modern plastic injection molding processes.
Challenges Of Multi Cavity Tooling
The downsides of include longer lead times for design and tooling, difficulty in making design changes, and the risk of having to discard the entire mold if one cavity becomes damaged or requires maintenance.
Additionally, multi cavity molds require precise balancing of the material flow to ensure all cavities fill evenly, which can be complex and time-consuming during the setup phase.
The increased complexity of the runner and gate system also raises the potential for defects such as short shots or warping if molding conditions are not optimized properly.
Material selection plays a critical role in multi cavity tooling as different plastic granules may behave differently under the same conditions, affecting the consistency of the molded parts.
Quality control becomes more challenging because defects in any single cavity can affect the entire batch, requiring careful inspection and monitoring throughout the production cycle.
Furthermore, the initial mold cost for multi cavity tooling is substantially higher than for single cavity molds due to the intricate design and precision machining required.
The ejector pins and cooling channels must be carefully designed and maintained to ensure uniform ejection and temperature control across all cavities.
Despite these challenges, the benefits of multi cavity molds in mass production often outweigh the difficulties, especially when producing large quantities of identical parts efficiently.
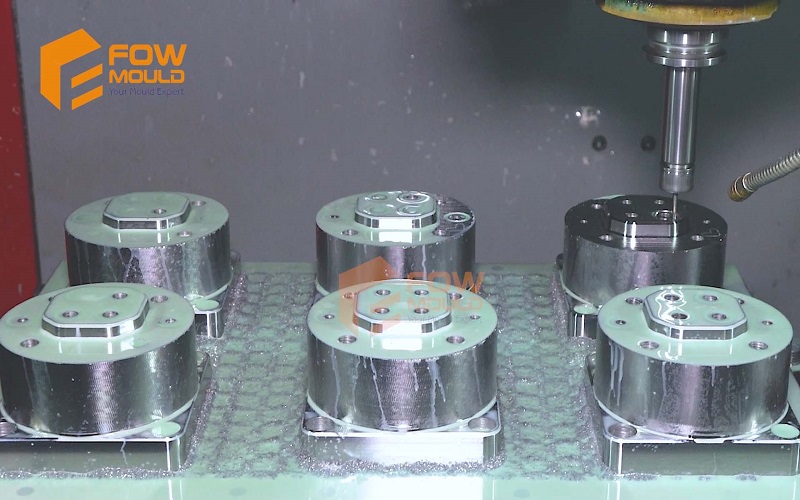
Single Cavity Mold vs Multi Cavity Mold
In the comparison between single cavity mold vs multi cavity mold, the main differences lie in production efficiency, cost, and applicable scenarios.
Production Efficiency
Single cavity molds: Produce only one product per cycle, resulting in relatively lower production efficiency, suitable for smaller volume demands.
Multi cavity molds: Capable of producing multiple products simultaneously in one injection molding cycle, significantly improving production efficiency. They can typically increase output by 60% to 80%, greatly shortening the production cycle.
Cost
Single cavity molds: Have lower initial investment costs, but due to limited production efficiency, the unit cost per product is higher. They are suitable for small batch or customized production.
Multi cavity molds: Although the initial investment is higher, their efficient production capacity allows costs to be spread over more products, significantly reducing the cost per unit, making them ideal for large-scale production.
Applicable Scenarios
Single cavity molds: Suitable for small batch production, sample making, and initial trial production stages. They have simple structures, low manufacturing costs, and high flexibility.
Multi cavity molds: Suitable for large-scale, efficient, and high-precision production needs. They have complex designs and require higher mold material quality and machining precision, capable of consistently producing high-quality products.
In summary, single cavity molds are suitable for small batch, complex, or customized products, while multi cavity molds are more appropriate for large-scale production to improve efficiency and reduce costs. The choice of mold type should be balanced based on product requirements and market scale.
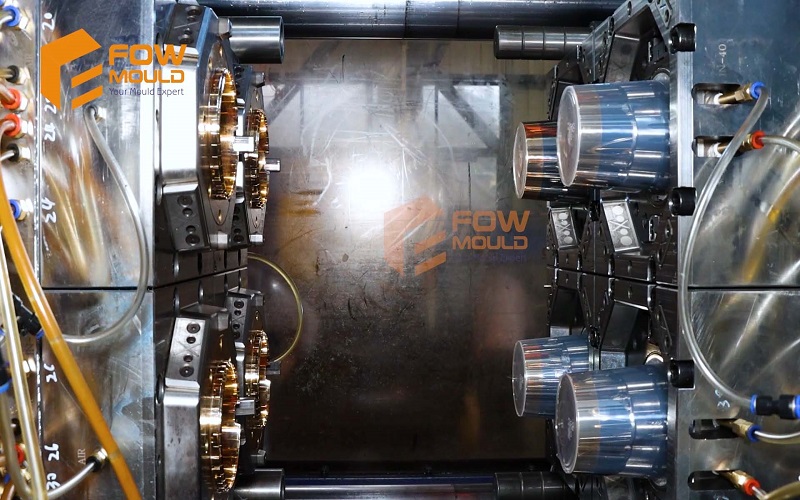
Conclusion
Multi cavity molds achieve the production of multiple parts in a single cycle by designing more than one cavity within a single mold. This not only greatly improves production efficiency and shortens the molding cycle but also effectively reduces the mold cost per unit product.
As an industry-leading mold manufacturer, FOWMOULD offers professional multi cavity mold manufacturing and injection molding services. If you are starting a new project, feel free to contact us for a free quote!