Plastic food containers are ubiquitous in modern life, from storage boxes in home kitchens to takeaway packaging containers. They are the preferred choice for food storage and transportation due to their lightweight, durability, and cost-effectiveness.
The quality of these containers directly impacts food safety, user experience, and the market competitiveness of manufacturing companies. At the core of this is the plastic container mould, which determines the shape, precision, and production efficiency of the containers.
Advanced mould design and manufacturing technology not only ensure that containers meet strict food safety standards but also optimize production processes, reduce costs, and increase output.
This article aims to explore the design and manufacturing technologies of plastic food container mould in-depth, analyzing their key processes, challenges, and future development trends to provide reference and inspiration for the industry.
What Is Plastic Food Container Mould?
A plastic food container mould is a specialized tool used in the injection moulding process to shape plastic materials into containers that meet specific requirements.
These moulds are essential for creating containers that are not only functional but also comply with food safety regulations. For example, those intended for water and other liquids, as well as plastic containers for deli products, take-away dishes, supermarket items and lots more.
The design of a plastic container mould takes into account factors such as wall thickness, durability, and the ability to withstand various temperatures and chemicals. Plastic containers can be hermetically sealed to prevent mold growth, which is ideal for edible products.
Some of the most common materials for food containers include polyethylene, styrene, and polypropylene. These plastics have a good resistance to chemicals and are durable.
By using advanced techniques and materials, manufacturers ensure that the finished product is both effective and efficient for storing and transporting food.
This process involves precise engineering to achieve the desired shape and size, making plastic food container moulds a critical component in the mass production of food containers.
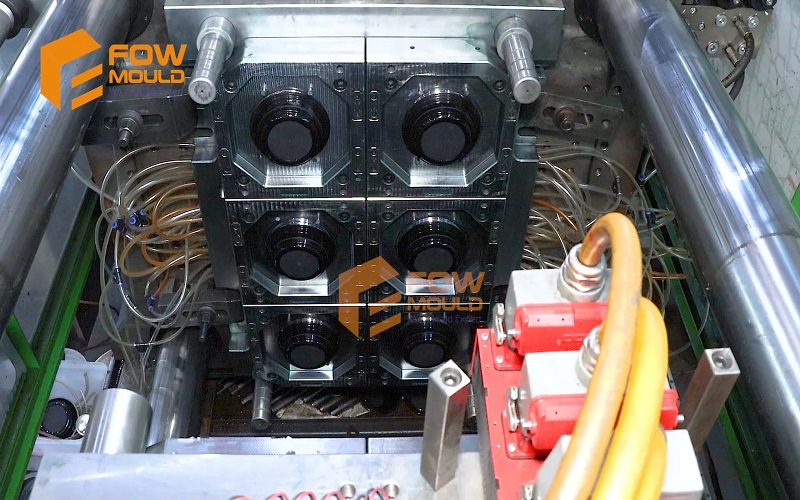
Characteristics Of Plastic Container Mould
Due to the specific application scenarios, plastic food container mould have the following notable characteristics:
Food Safety Requirements
Since they come into direct contact with food, the manufacturing of moulds must comply with strict food safety standards, such as those set by the U.S. FDA (Food and Drug Administration) or the EU’s regulations on materials in contact with food (EC No 1935/2004).
The surface of the container mould must be smooth and free of burrs to prevent residue buildup that could harbor bacteria, and the materials must not release harmful substances, ensuring the containers are safe and non-toxic.
High Precision and Complex Geometries
The food container mould has the characteristic of good packaging effect, various types, colorful.
Food containers often require complex designs, such as sealed lids, compartment structures, or thin-wall features. Moulds must support high-precision processing to ensure consistent container dimensions and excellent sealing performance.
Durability and High Output Demand
Food container production is typically a high-volume manufacturing process, requiring moulds to withstand tens of thousands to hundreds of thousands of injection cycles.
Therefore, mould materials must possess high strength, wear resistance, and corrosion resistance to extend their lifespan, while optimizing cooling and demoulding systems to shorten the forming cycle and increase production efficiency.
These characteristics collectively ensure that plastic food container moulds meet functional requirements while supporting efficient and cost-effective large-scale production.
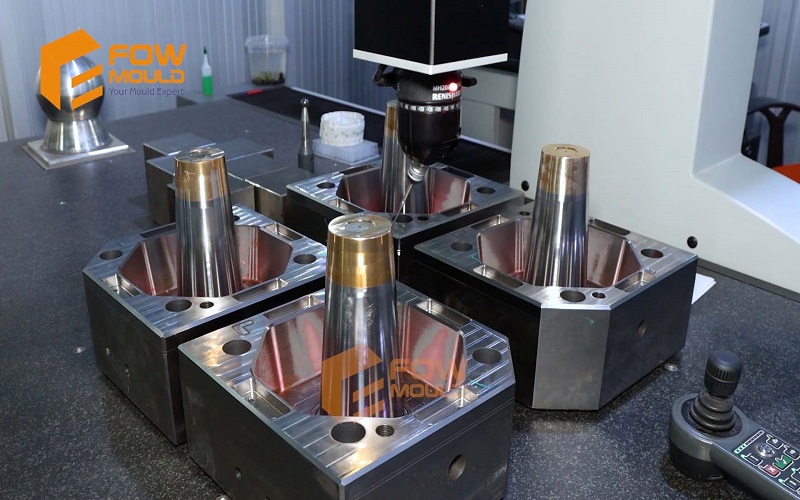
Design Tips of Plastic Food Container Mold
The design of plastic food container moulds is a complex and meticulous process that involves multiple critical factors to ensure the quality and performance of the final product. Below are the key considerations for designing plastic food container molds:
1. Material Selection
Selecting the appropriate mold material is fundamental to the design process, as it directly impacts mold longevity, cost, and product safety. Food container mould manufacturers use materials in the mould construction should be non-toxic and resistant to chemical reactions that could affect the food.
Common Mold Materials:
P20 Steel: A pre-hardened mold steel suitable for medium-volume production, offering excellent machinability and polishability, commonly used for single-cavity or multi-cavity food container molds.
718 Steel: An upgraded pre-hardened steel with superior hardness and wear resistance compared to P20, ideal for high-volume molds, particularly for thin-wall container molds.
Stainless Steel (e.g., 420 or H13): Known for excellent corrosion resistance and high-temperature tolerance, suitable for molds requiring high surface finish and strict food safety compliance, such as those for sealed containers.
2. Mold Structure Design
The structural design of the container mold directly affects production efficiency and product quality. Designers must consider the cooling system, demolding mechanism, and gating system to optimize the manufacturing process. A well-designed structure can significantly reduce cycle times and enhance production efficiency.
Single-Cavity vs Multi-Cavity Mold:
Single-Cavity Mold: Produce one container per cycle, suitable for low-volume, customized, or complex designs (e.g., specialty gift containers). Advantages include simpler design and easier adjustments; disadvantages include lower production efficiency.
Multi-Cavity Mold: Produce multiple containers simultaneously, ideal for large-scale production (e.g., disposable lunch boxes). Advantages include high efficiency and lower per-unit costs; disadvantages include complex design and the need to ensure uniform filling across cavities.
Cooling System:
Design Considerations: Cooling channels must be evenly distributed and positioned close to the mold cavity to ensure uniform cooling; thin-wall container molds require denser channels to prevent deformation.
Impact: An optimized cooling system can reduce cycle times by 20%-30%, significantly improving production efficiency and minimizing defects like sink marks.
Technological Trends: The use of 3D printing to create complex cooling channels (e.g., conformal cooling) further enhances cooling efficiency.
Demolding Mechanism and Ejection System:
Ejection System: Utilizes ejector pins, plates, or air-assisted mechanisms, with ejection points optimized based on container shape to avoid surface damage.
Angled Lifters and Sliders: Employed for complex geometries (e.g., containers with snap-on lids) to ensure smooth demolding of side features.
Surface Treatment: High-polish mold surfaces combined with appropriate release agents reduce demolding resistance, improving product surface quality.
3. Precision and Tolerances
Plastic food containers require high-precision dimensions and shapes to ensure reliable sealing performance and user satisfaction.
Designers extensively use CAD/CAE software (e.g., Moldflow) to simulate the injection molding process, including melt flow, cooling, and deformation, optimizing the mold structure to achieve consistent product dimensions and complex geometries. This digital approach enhances mold accuracy and minimizes defects.
4. Hot Runner System
The choice of hot runner system depends on the container’s shape, material properties, and production scale.
For instance, thin wall containers may require multi-point hot runners to ensure uniform filling, while complex-shaped containers may need valve-gated hot runners to control flow precisely.
By carefully selecting and optimizing the hot runner system, manufacturers can enhance the efficiency and quality of the molding process.
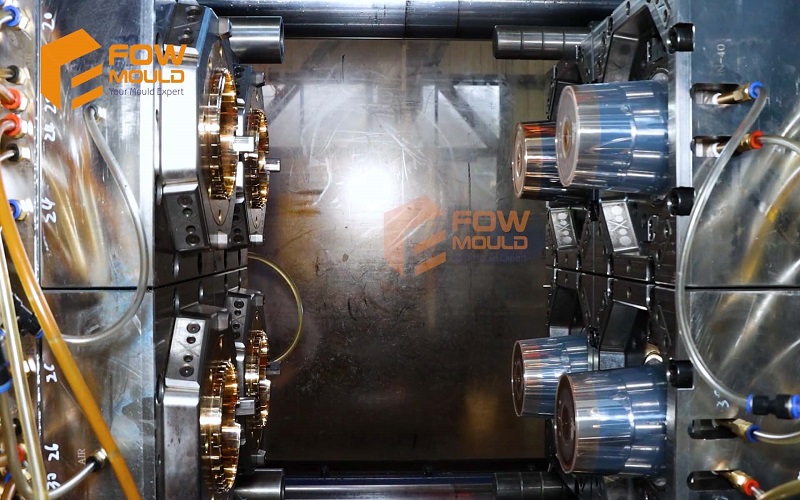
Processing Methods Of Plastic Food Container Mould
The production of plastic food containers relies on various molding techniques, each tailored to specific container designs, material properties, and production requirements.
Plastic injection moulding is just one technique that is commonly used, along with blow moulding , extrusion moulding and more.
Injection Moulding
Commonly used for producing high-precision food containers such as lunch boxes, deli containers, microwave-safe containers, and sealed storage boxes.
In particular, thin wall injection molding is a specialized process that focuses on creating containers with very thin walls, typically less than 0.8mm thick.
Blow Moulding
Used for producing hollow plastic food container, such as bottles and jars. In this process, plastic is melted and formed around a mould through the use of pressurized air.
Extrusion Molding
It is often combined with other processes like thermoforming for food containers.It used for producing simple food containers like trays, lids, or shallow packaging for deli items and baked goods.
Future Development Of Food Container Mold
The future development of food container molds is driven by the demand for sustainability, intelligence, and efficiency. Here are the main trends:
Sustainability
Biodegradable and Recyclable Materials: Mold designs are adapting to biodegradable plastics (like PLA) and recycled plastics (such as rPET), supporting the production of eco-friendly containers and aligning with the requirements of a circular economy.
Eco-Friendly Mold Materials: The use of durable, recyclable steel or low-impact coatings extends mold life and reduces resource consumption.
Intelligence
Smart Molds: Integration of sensors to monitor parameters like temperature and pressure in real-time, optimizing production and predicting maintenance needs to minimize downtime.
Industry 4.0 Applications: Combining IoT, AI, and data analytics to optimize mold design, enable remote monitoring, and automate production, enhancing efficiency and flexibility.
Lightweight and Thin-Wall Technology
Thin-Wall Technology: Developing high-precision molds and conformal cooling channels to meet the high-pressure and rapid molding needs of thin-walled containers (0.4-0.8 mm), reducing material usage.
Technological Breakthroughs: Utilizing high-strength materials and CAE simulations to address issues like warping and uneven filling, ensuring the strength and functionality of lightweight containers.
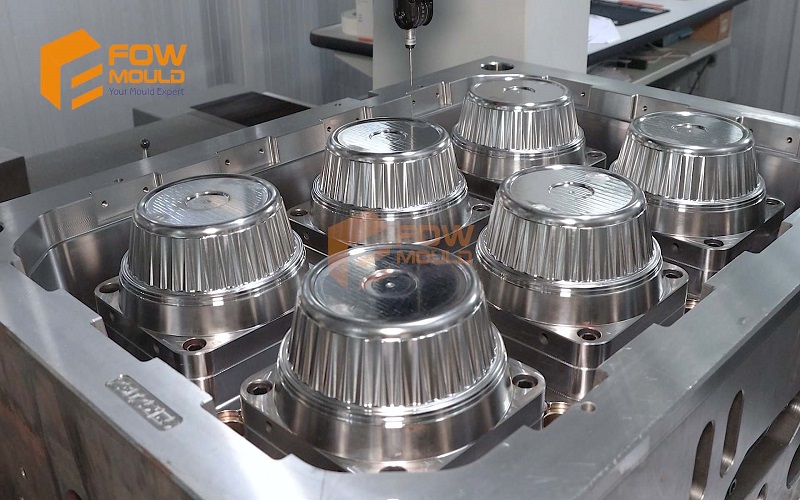
Conclusion
Plastic food container molds are a critical core technology in the food packaging industry, leveraging precise design and diverse processing methods to meet a wide range of needs, from disposable lunch boxes to reusable storage containers.
Their design must balance food safety, production efficiency, and cost control while aligning with trends such as sustainability, intelligence, and lightweighting, ensuring compliance with stringent food contact standards and minimizing environmental impact.
If you are looking to customize a high-quality plastic container mold, contact FOWMOULD today! As a leading injection mold manufacturer in China with over 40 years of extensive experience, we are dedicated to delivering innovative, reliable, and eco-friendly mold solutions to help your products stand out in the market!